How tracking returnable packaging can solve supply chain and logistical challenges
Overcoming Some Returnable Packaging Challenges
The management and tracking of returnable packaging in supply chain and logistics operations present significant challenges for organizations. Despite these complex challenges, efficient management of returnable assets can bring tremendous advantages and value to any operation. Returnable packaging, such as pallets, crates, containers, and totes, plays a crucial role in reducing waste, improving sustainability, and optimizing the overall supply chain efficiency. However, efficiently managing and tracking these assets can be a complex and costly task, leading to various issues and inefficiencies:
- Loss and Theft: Returnable packaging items are often lost or stolen during transit or storage, resulting in financial losses and disruptions to the supply chain.
- Inefficient Utilization: Organizations struggle to ensure that returnable packaging is used optimally, leading to excess inventory or shortages of these assets.
- Manual Processes: Many companies still rely on manual processes, such as paper records or spreadsheets, to track returnable packaging, which are error-prone and time-consuming.
- Lack of Visibility: Limited visibility into the location and status of returnable packaging can lead to delays, increased transportation costs, plant equipment downtime, manual repacking from expendable, and customer dissatisfaction.
- Maintenance and Repairs: Ensuring the returnable packaging is in good condition requires regular maintenance and repairs, which are often not properly managed.
- Reverse Logistics: Managing the return journey of packaging items back to the origin can be complex and costly. Companies must coordinate transportation, inspection, and storage of returned items.
- Compliance and Accountability: Compliance with returnable packaging agreements and contracts can be challenging, and organizations may struggle to hold partners and suppliers accountable for lost or damaged items.
- Sustainability Goals: Organizations aiming to reduce their environmental footprint and meet sustainability goals need better tracking and management systems for returnable packaging.
To address these challenges, organizations need innovative solutions that leverage technology such as RTLS, GPS and Bluetooth (BLE) with advanced data analytics. These solutions should provide real-time visibility into the location, condition, and usage of returnable packaging, automate tracking processes, and facilitate better collaboration with partners and suppliers.
The objective is to develop a robust and efficient returnable packaging tracking system that not only reduces costs and losses but also contributes to sustainability goals, improves customer satisfaction, and streamlines supply chain operations. Although the challenges can seem overwhelming, a large suite of actions are not only available and investable today, but companies are in a position to deliver and support it.
Discover the Pozyx Platform
The Pozyx Platform brings indoor and outdoor positioning data together to provide full asset visibility, automation and location-based insights for logistics and manufacturing.
Pozyx Platform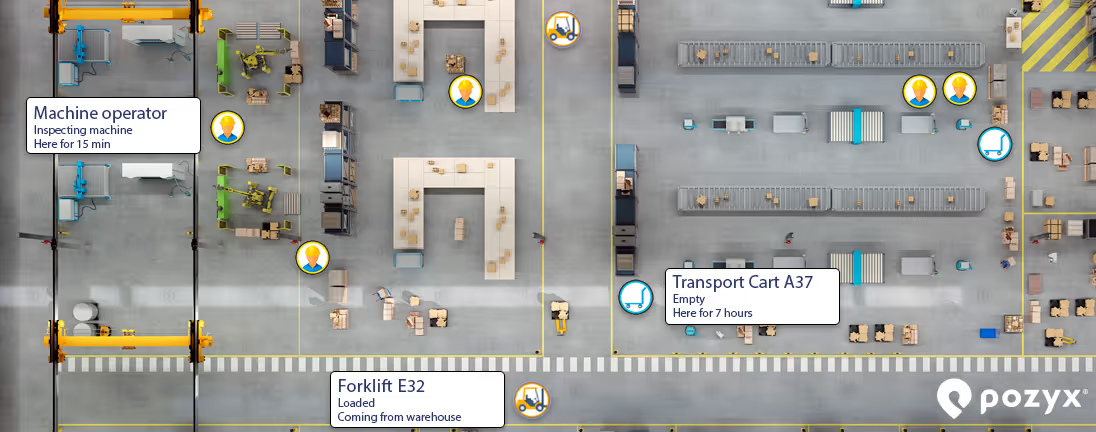
Solution for tracking returnable packaging
To address the challenges associated with tracking returnable packaging in the supply chain, organizations can implement a comprehensive solution that combines technology, processes, and best practices.
1. Indoor and outdoor tracking:
Throughout its lifecycle, a returnable package can be on the road, in a storage faciliy or at a customer. Hence, it is required to provide both outdoor and indoor tracking to provide full visibility at all times.
• Equip returnable packaging with UWB or GPS and BLE tags to enable real-time tracking and monitoring of their location, condition, and usage.
• These UWB or GPS sensors can provide data on factors like temperature, humidity, and shock, ensuring the quality and integrity of the packaging.
Not every technology is the right fit for a specific returnable packaging problem. Depending on scale, indoor/outdoor usage and ability to install infrastructure, one technology may be more suitable than the other. In some cases, a combination of technologies is required. An overview of different location technologies can be found in the following post.
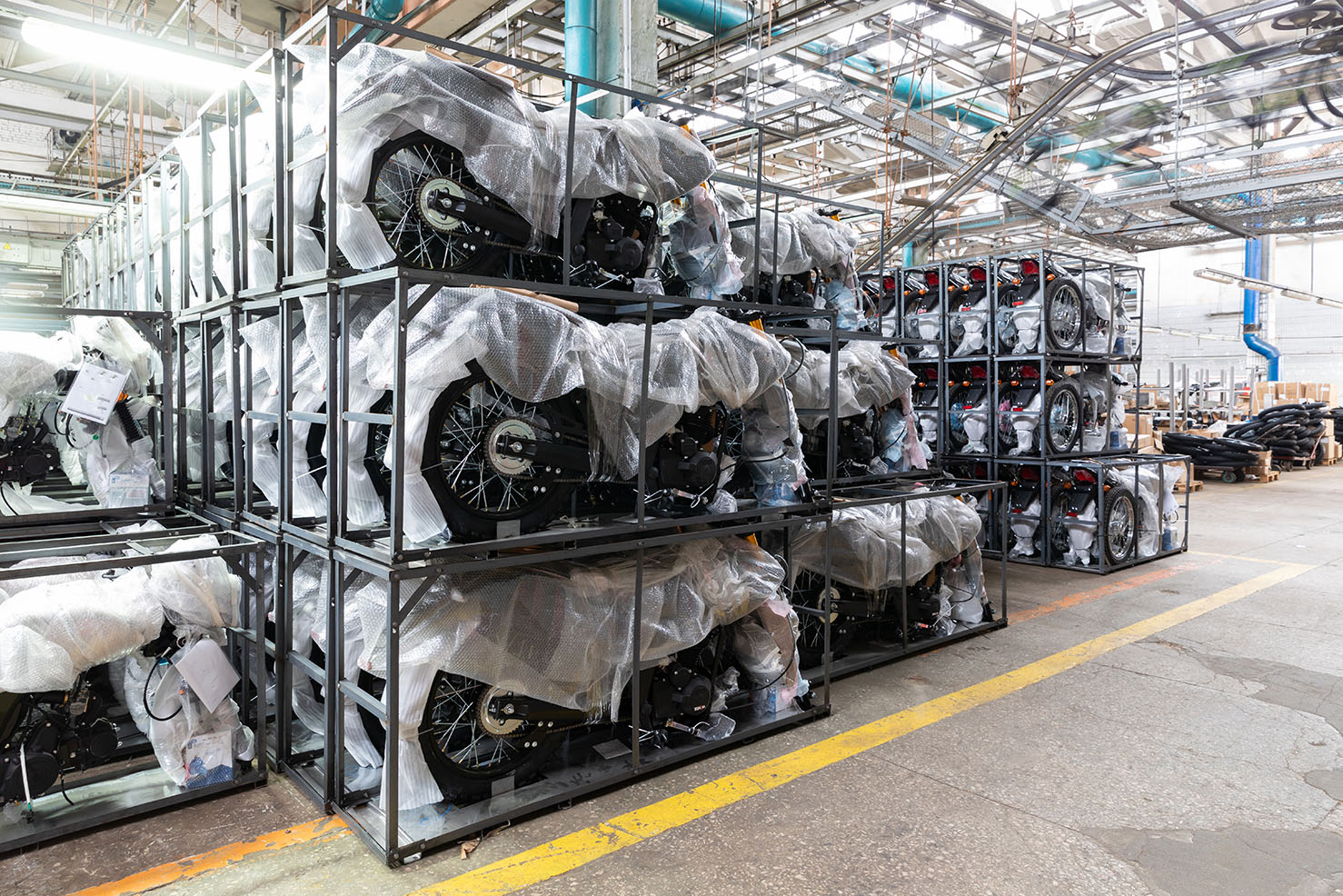
2. Centralized Tracking Platform:
• Implement a centralized tracking platform or software that aggregates the data.
• This platform should provide a user-friendly interface for users to access real-time information about returnable packaging assets.
3. Automated Data Collection:
• Automate the collection of data from UWB, GPS and BLE tags to reduce human error and streamline tracking processes.
• Utilize cloud-based solutions for data storage and accessibility.
4. Data Analytics and Reporting:
• Employ data analytics to derive actionable insights from the collected data using smart technology and learning with AI integration.
• Generate reports and dashboards that offer visibility into the utilization, condition, and history of returnable packaging items.
• Use predictive analytics to forecast future needs and prevent losses or inefficiencies.
5. Alerts and Notifications:
• Implement an alert system that sends notifications to relevant stakeholders when specific events occur, such as when returnable packaging items are nearing their maintenance schedule or when they deviate from their expected route.
• Integrate the alert system with plant/ facility And on system for immediate notification of miss shipment potential.
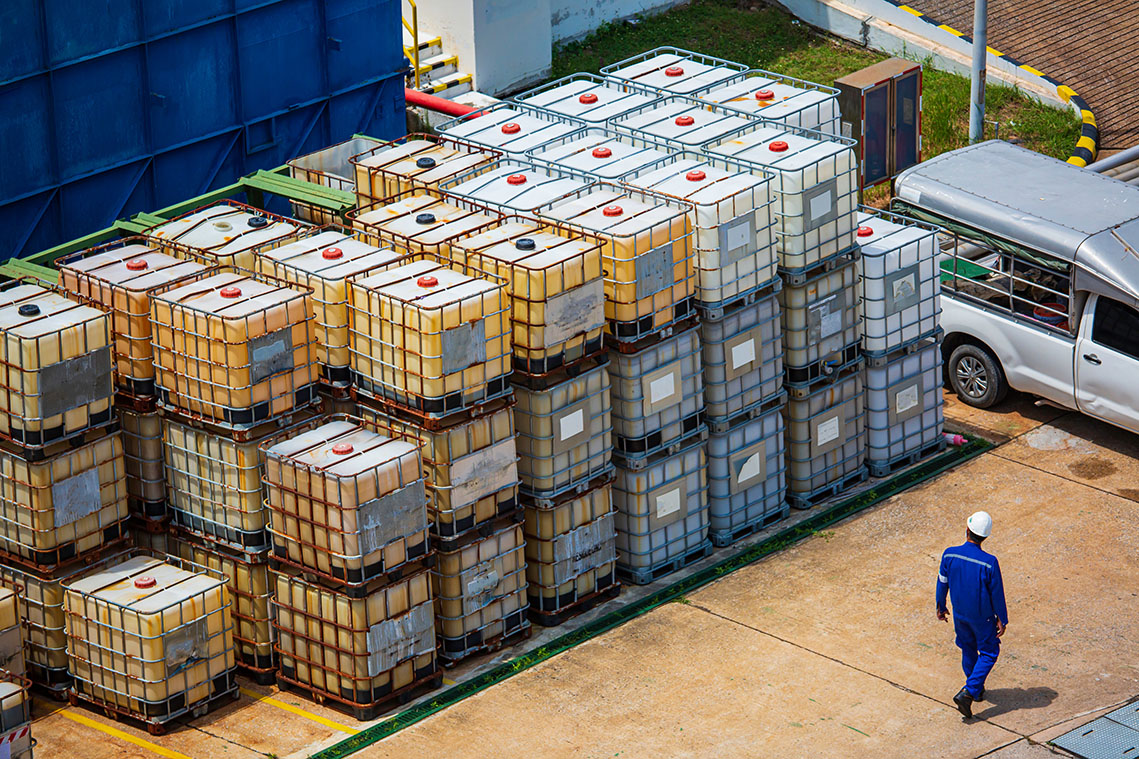
6. Integration with Supply Chain Systems:
• Integrate the tracking solution with existing supply chain management systems, including transportation management (TMS) and inventory management systems (WMS).
• This integration ensures that data on returnable packaging is seamlessly incorporated into broader supply chain operations, including route optimization and reverse logistics planning.
7. Maintenance and Repair Tracking:
• Implement a module within the tracking system to manage the maintenance and repair schedules of returnable packaging items.
• Ensure that damaged items are promptly identified, tagged, logged, and scheduled for repair or replacement.
8. Collaboration and Partner Engagement:
• Foster collaboration with suppliers, logistics partners, and customers by providing them with limited access to the tracking system.
• Enable partners to update the system with relevant data, such as the return of packaging or damage.
9. Sustainability and Cost Reduction:
• Leverage the data and insights from the tracking system to optimize the use of returnable packaging, reduce losses, and minimize transportation costs.
• Support sustainability initiatives by promoting the reuse and recycling of packaging materials.
10. Continuous Improvement:
• Continuously monitor the performance of the tracking system and gather feedback from users and partners to make necessary improvements and enhancements.
Conclusion
Implementing a comprehensive returnable packaging tracking solution like this can lead to improved efficiency, reduced costs, enhanced sustainability, and better compliance with returnable packaging agreements. It also positions organizations to meet the evolving demands of the supply chain and logistics industry.
If you want to learn more about the Pozyx solution for managing returnable packaging, please visit our solution page.
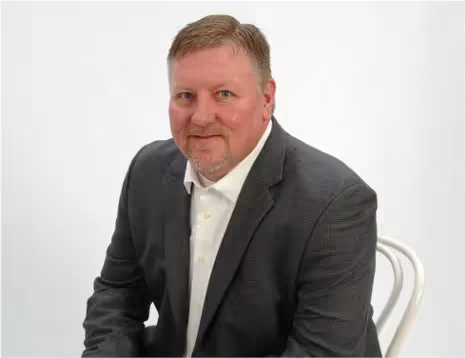
Written by
Rick Graham
Partner of Pozyx
Over 30 years experience in the distribution and automotive industry, with proven Senior Leadership for many of those years. An extensive background in Operational Analysis and Solution Implementation. Having deployed solutions at over 100 locations around the world, all delivering positive P&L impact. A certified John Maxwell Team Speaker, Coach and Mentor.