Lean Manufacturing Solutions
Lean transformation in manufacturing strives to create a culture of continuous improvement, eliminating waste and reducing costs. Control over production processes and real-time insights on product flows are the building blocks of lean optimization. Pozyx’s RTLS tracks and analyzes moving assets, people, and WIP to discover issues that relate to the 8 wastes of lean manufacturing.
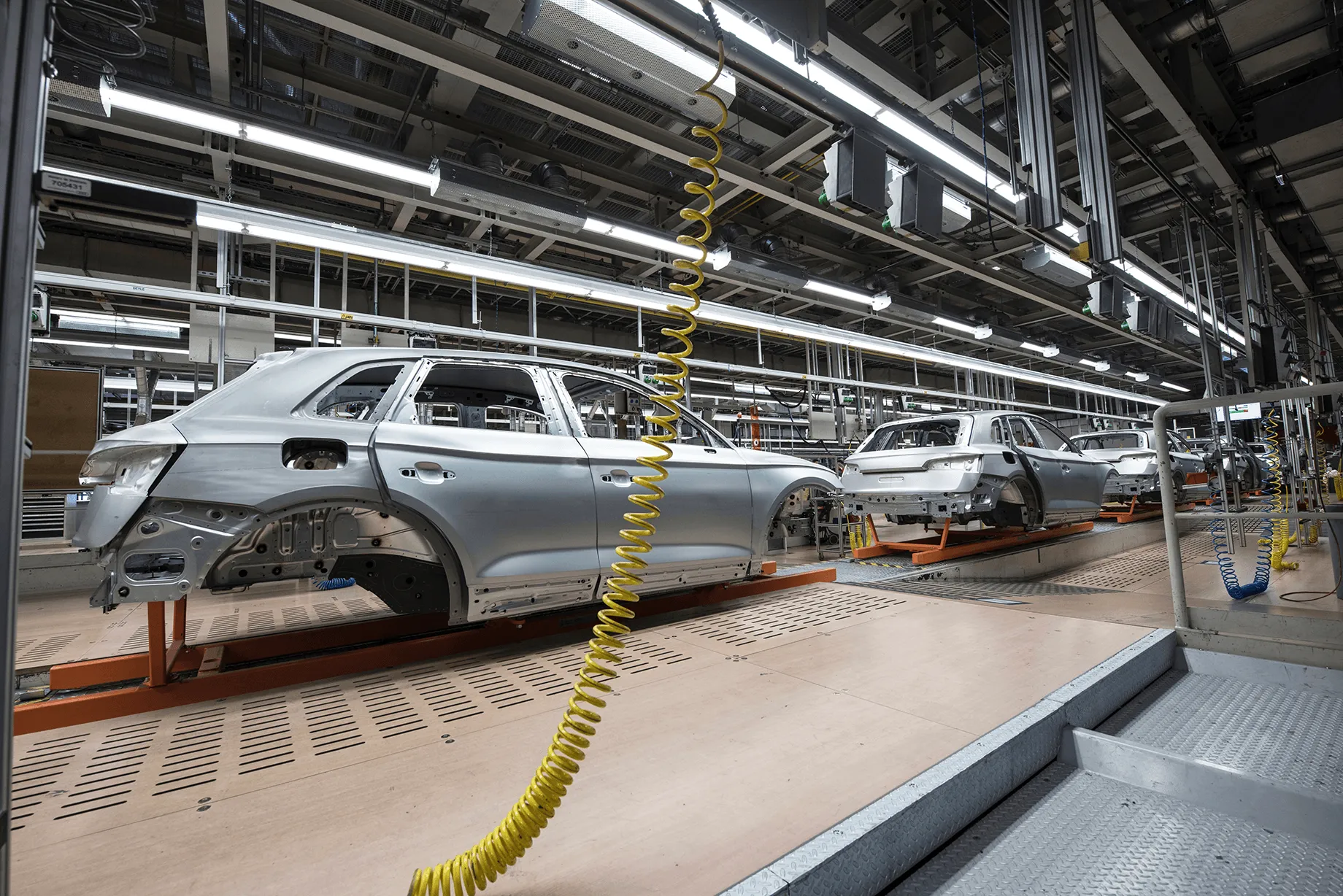
How RTLS addresses the 8 wastes in lean manufacturing
Defects
Detect faulty assets and deviations from the target product state. Prevent re-introduction in the production cycle.
Over
production
Keep track of WIP to avoid goods lost and re-ordered, avoiding increased costs and excess inventory.
Waiting
Measure waiting time of WIP to gather accurate data and identify improvements to the production flow and avoid down time.
Transportation
Map distance traveled by goods, orders, and operators and detect improvement opportunities to reduce operational costs.
Inventory
Locate inventory to prevent lost positions, resulting in excess stock, inventory build-up, increased storage space and higher cash flow.
Motion
Introduce spaghetti charts tracking operator or robot movements and indicate how motion flows can be improved.
Over processing
Keep track of orders in real time and provide accurate individual work instructions in MTO environments to avoid unnecessary manufacturing process components.
Unused talent
Automated location data reduces the need for manual time studies by industrial engineers, creating more time to spend on analyzing and improving processes.
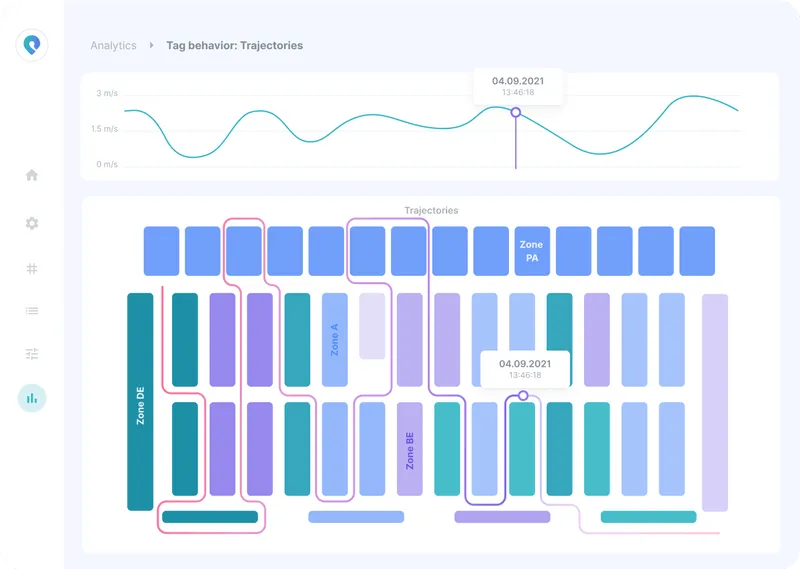
Lean manufacturing made painless
The effective way to reduce waste, boost profits, and achieve operational excellence
The lean manufacturing system aims to maximize product value while minimizing waste without sacrificing productivity. Using the Pozyx RTLS in lean manufacturing provides accurate real-time location data of assets in the production flow, as input for value stream mapping, adhering to the Kaizen methodology and applying Six Sigma and SMED (Single Minute Exchange of Dies & Quick Changeover) techniques.
- Pinpoint the exact location of materials and products throughout the whole production process
- Automated time studies and insightful analytics
- Optimize inventory management, avoid manual audits
- Obtain transparency on materials, reduce asset loss and avoid goods lost
- Collect actionable data for quality control and efficiency checks
- Plot process mapping to fuel performance metrics
Map asset performance
- Unlock asset performance data to raise OEE (overall equipment effectiveness)
- Measure asset and process down time, reduce downtime risks
- Analyze and fix inconsistent and inefficient workflows
- Avoid inefficient wastes in motion & transportation
Real-time issue visibility
- Spot bottlenecks and prevent disruptions
- Minimizing downtime, setup and changeover time
- Correct missing goods issues and manage inventory more effectively, avoid unnecessary WIP & excess stock
Efficiency checks
- Analyze policy performance and compliance levels
- Make quick decisions based on real-time data and maximize uptime
- Track movement and stock in processes, at batch and at item level
- Introduce eKanban WIP control