Interoperability with VDA5050 for full intralogistics visibility
Pozyx and VDA5050
Pozyx is excited to announce that its real-time visibility platform now supports the VDA5050 standard for autonomous mobile robots (AMRs). VDA5050 is an interoperability standard to track and control AMRs or AGVs (automated guided vehicles) from different vendors through a single standardized communication interface.
By combining VDA5050 with the omlox RTLS standard, which offers a standardized interface for outdoor and indoor location systems, the Pozyx Platform enables complete visibility of all vehicles and assets within a supply chain. This includes not only AGVs and AMRs but also forklifts, tugger trains, trolleys, and even operators, ensuring a more efficient and streamlined approach to asset management.
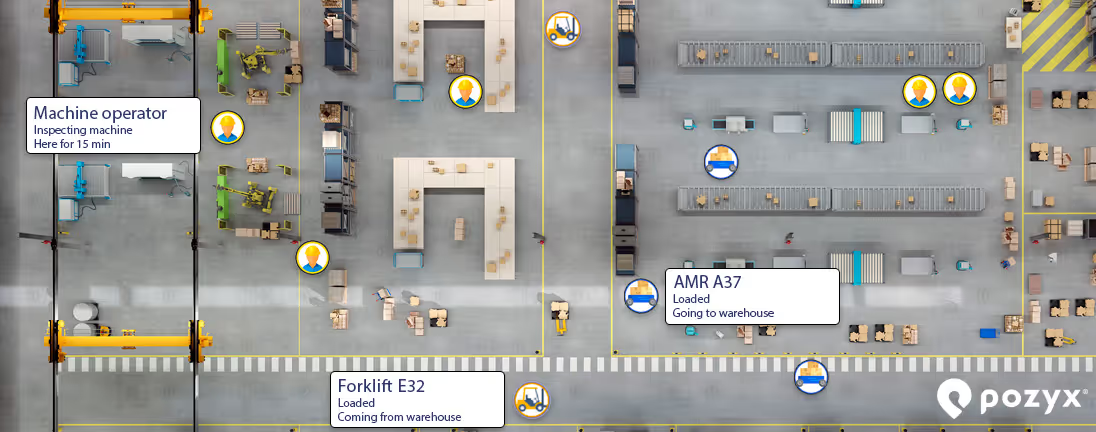
AMRs are increasingly being used in operations due to their ability to improve efficiency, reduce labor costs, and navigate dynamic environments without needing fixed infrastructure. However, they often operate in collaboration with non-automated vehicles like forklifts or tugger trains, as well as with human workers.
The integration of AMRs with non-automated vehicles in intralogistics creates challenges related to traffic coordination and workplace safety, as different systems and entities must navigate shared spaces without collisions or delays. Additionally, managing mixed environments with both automated and manual processes can complicate workflow synchronization and reduce the overall efficiency if not properly optimized. These are exactly some of the issues that the Pozyx platform aims to resolve by integrating with the VDA5050 protocol.
Short Introduction to VDA5050
VDA5050 is an upcoming standard for AMRs and AGVs which standardizes how they can be controlled and how they can provide status information. VDA5050 is the result of a collaboration between the German Association of the Automotive Industry (VDA) and the VDMA Materials handling and Intralogistics Association. VDA 5050 allows managing vehicles with proprietary AGV controls from different vendors directly via a standardized Interface (VDA5050) with a Universal Master Control (fleet control).
The standard is being supported by various manufacturers including Jungheindrich, Bosch Rexroth, and Still.
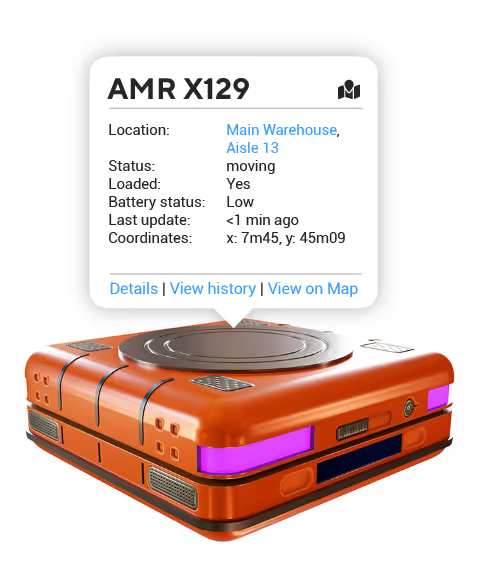
Through the VDA5050 standard, it is possible to remotely command the AMR’s.
From a status point of view, the VDA5050 standard provides:
- AMR location data
- AMR velocity and orientation
- AMR status: idle or moving
- AMR load status and load identification (if available)
Combining VDA5050 with Real-time Location Systems
VDA5050 is typically considered as a standard interface between the driverless transport system and the control system (the so-called fleet controller). The fleet controller will send commands to the fleet of AMR’s using the VDA5050 protocol. This includes routing, pick up commands, emergency stops and more. At the same time, the fleet controller will receive real-time updates on the robot’s status including location, velocity and load information.
With VDA5050, json messages are sent over the MQTT protocol and can be received by different software components simultaneously. Through a small protocol translator, the VDA5050 message structure can be translated to the Omlox Hub standard.
An omlox hub is a central software component in the omlox ecosystem that enables the seamless integration and management of real-time location data from various tracking technologies (such as UWB, GPS, RFID, and BLE) in a unified system. It acts as a middleware that gathers location information from different devices and systems, standardizes it, and makes it available to applications, enabling accurate and efficient indoor and outdoor tracking within smart factories and logistics environments.
By feeding AMR location data to the omlox hub it is possible to obtain full visibility of all vehicles such as AGV’s, AMR’s, forklifts and tugger trains, but also visiblity of operators, push carts, containers and more. While the AMR’s and AGV’s can self-localize, the other assets can be tracked with a real-time location system such as an UWB RTLS.
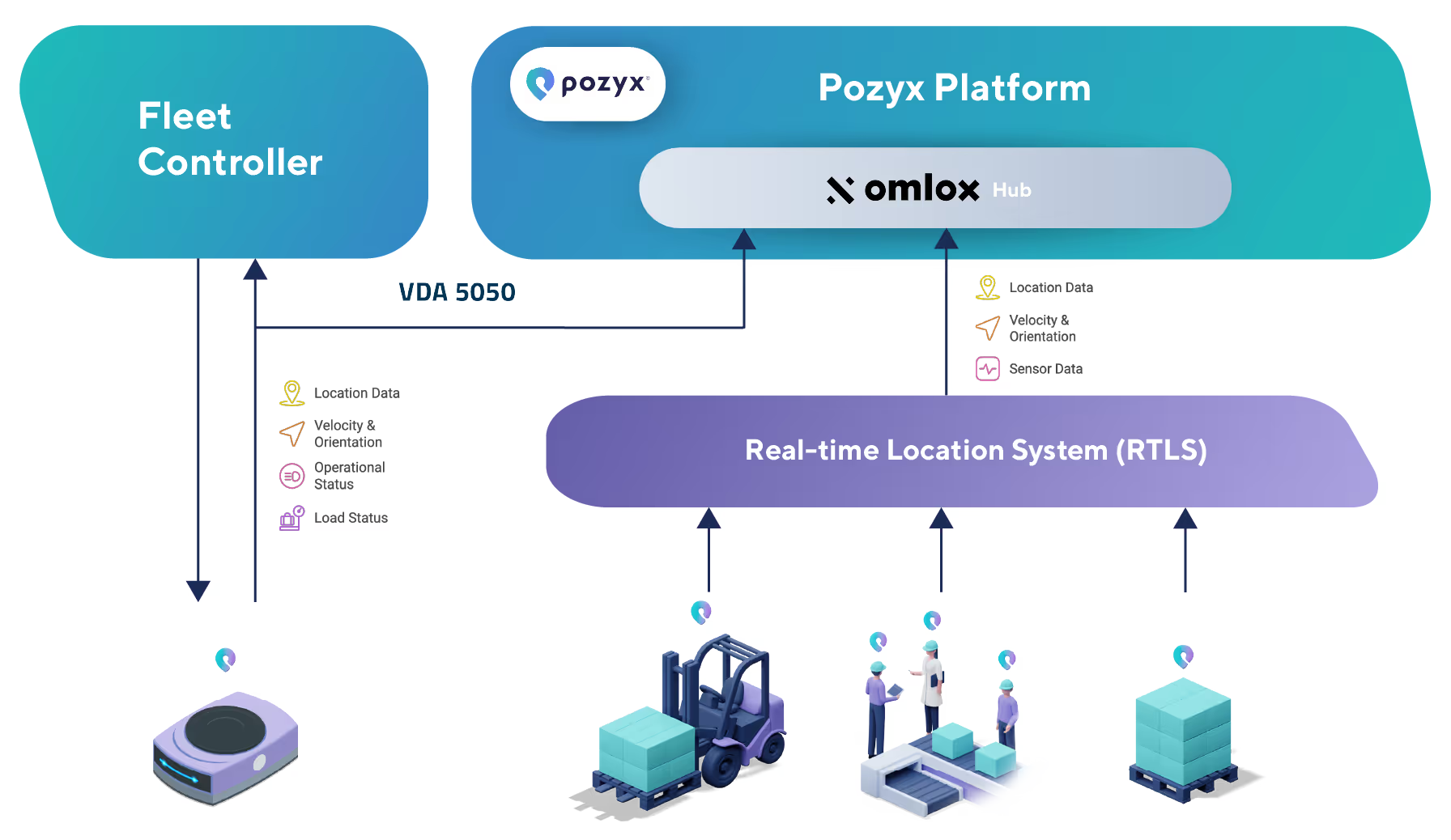
Discover the Pozyx Platform
The Pozyx Platform brings indoor and outdoor positioning data together to provide full asset visibility, automation and location-based insights for logistics and manufacturing.
Pozyx Platform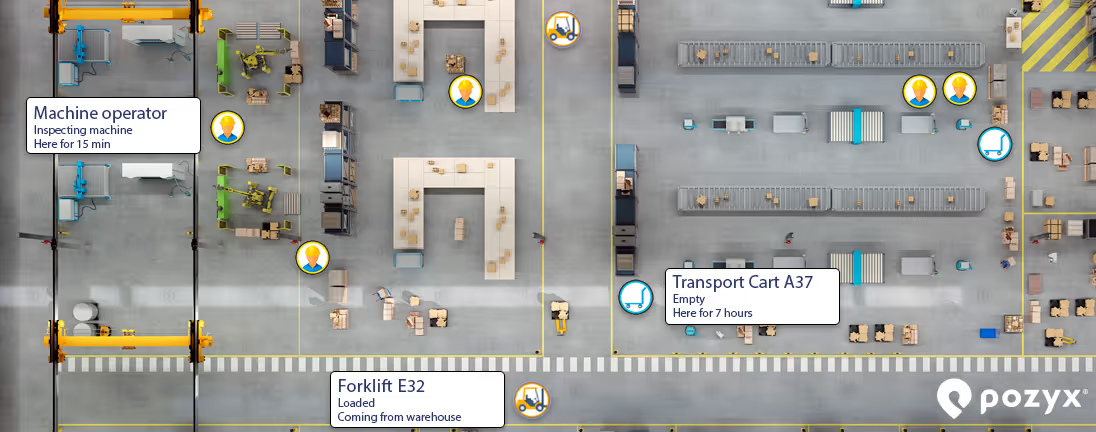
Benefits of Using VDA5050 Together with RTLS
Fleet Performance
- Gain insights into fleet and robot operations over extended periods through comprehensive data dashboards.
- Track key performance indicators (KPIs) like distance traveled, completed trips, and vehicle utilization rates across your facilities.
- Pinpoint specific events, troubleshoot unexpected workflow interruptions, and optimize fleet utilization to ensure maximum efficiency.
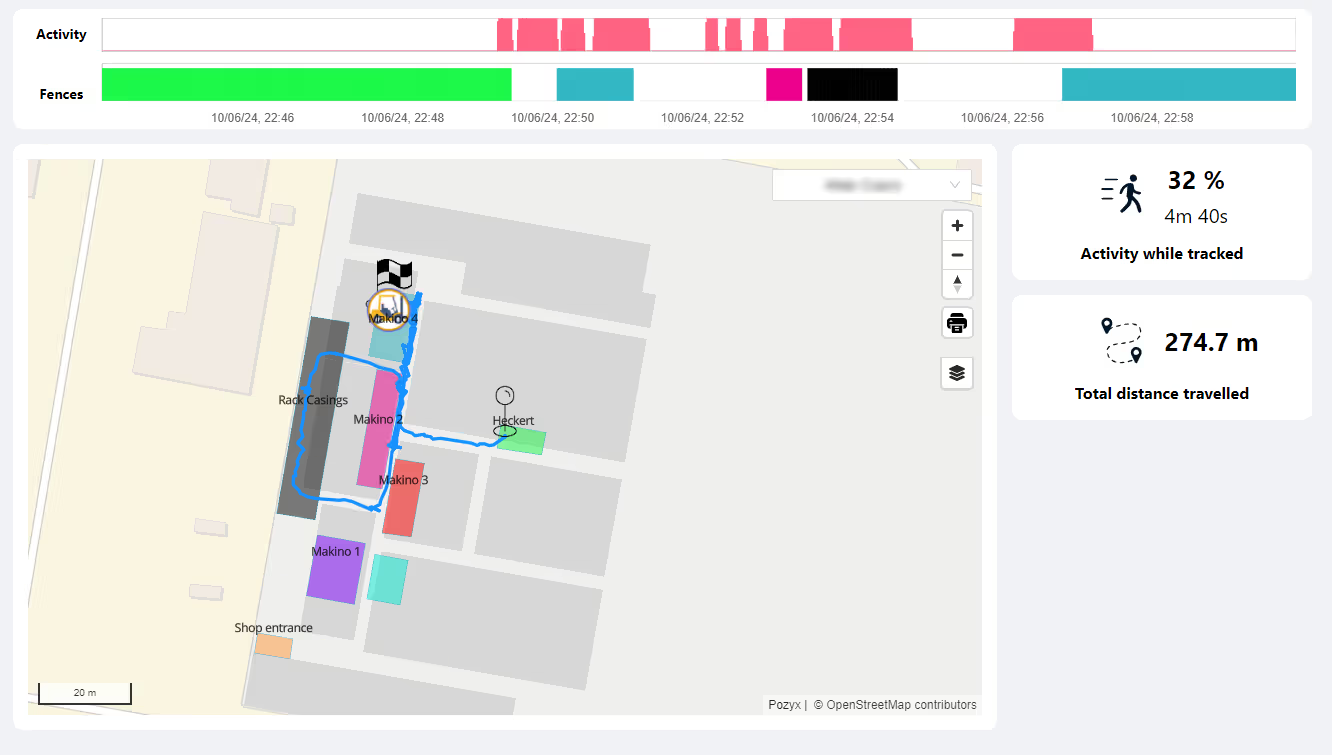
Traffic Analysis and Optimization
- Visualize the movement of robots and forklifts throughout your facility using heatmaps to identify traffic patterns.
- Monitor high-traffic areas during peak times to enhance your intralogistics and reduce potential bottlenecks.
- Delve into specific traffic scenarios or incidents to analyze root causes and improve overall traffic flow.
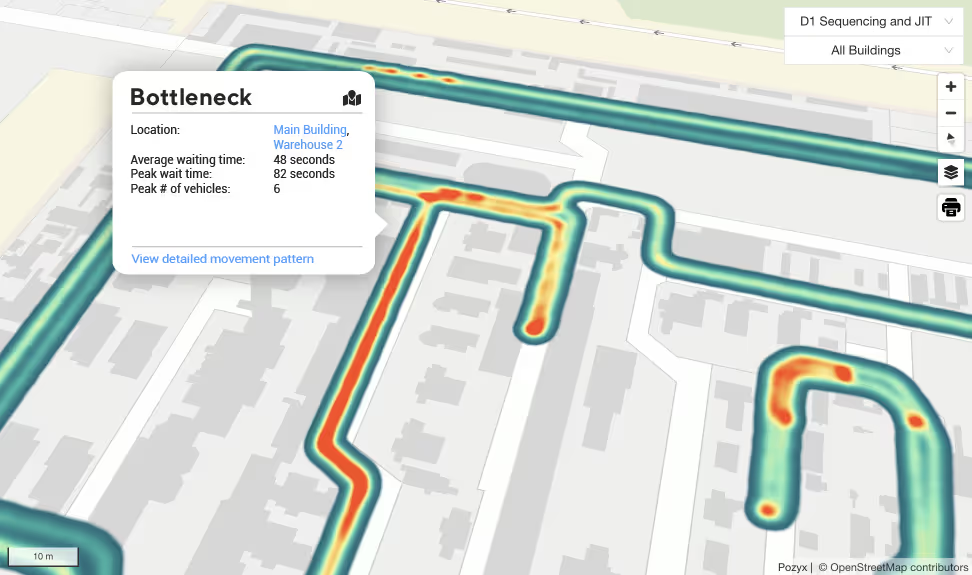
Safety
- Manage traffic lights and signage by monitoring all moving vehicles and pedestrians within your operation to minimize the risk of collisions.
- Automatically shut down heavy or dangerous machinery when robots, vehicles, or pedestrians are detected in proximity, enhancing workplace safety.
Unified API
- Access a unified API that enables seamless industry 4.0 integration and control of all moving assets within your operation, simplifying system management and coordination.
- Access to unified reports for all moving assets that can be integrated into dashboarding tools like Power BI or Tableau.
How an AGV or AMR Determines its Location
In the VDA 5050 protocol, the robot's location, orientation and velocity is available and provided by the robot. AGVs and AMRs typically determine their location using a combination of sensors and technologies. They often rely on LiDAR, cameras, and ultrasonic sensors to map their surroundings and navigate through complex environments. Additionally, AMRs may use GPS or indoor positioning systems, such as RFID or ultra-wideband (UWB), to achieve precise localization. These technologies enable AMRs to move autonomously, avoid obstacles, and adjust their paths in real-time while maintaining accurate positioning.
AGVs have less advanced location systems and typically use guidance lines or markers on the floor to get a sense of location. They would then follow the lines on the floor, or recalculate their position every time they move over a marker on the floor.
Conclusion
As we've explored, VDA5050 is more than just a protocol - it's the foundation for the future of automated logistics! In combination with real-time location systems, it is possible to obtain full visibility of all moving assets within your facility. Leveraging VDA5050 and RTLS can improve fleet performance, intralogistics traffic, safety and system integration.
Whether you're managing a small warehouse or a massive manufacturing facility, implementing VDA5050 and RTLS can dramatically improve your operations. Ready to take the next step? Reach out to our experts for more details!
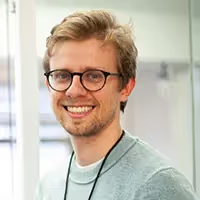
Written by
Samuel Van de Velde
CTO & Co-Founder at Pozyx
Samuel is an electrical engineer with a strong interest in location technology. Skilled in Entrepreneurship, Public Speaking, Product Management, internet of things (IoT), and Machine Learning. After graduating In 2010, he joined the Department of Telecommunications and Digital Information Processing (TELIN) to pursue a Ph.D. degree on the topic of collaborative indoor localisation. In 2015, he founded the spin-off company Pozyx out of that research.