What are the 8 wastes in lean manufacturing and how to reduce them
Efficiency is the essence of every manufacturing environment and yet there is still enormous potential for improvement. Every business should make it their priority to eliminate waste in industrial processes. But how can those areas be identified and addressed?
Lean Manufacturing is a production methodology focused on maximizing productivity while reducing waste. In lean manufacturing, the 8 wastes are identified as overproduction, waiting, unnecessary motion, over-processing, excess inventory, unnecessary transport, defects, and unused talent. These wastes lead to inefficiencies and increased costs in manufacturing.
The Pozyx real-time location solution can address these wastes by providing accurate and real-time data on the location of material and equipment and the analysis of their movement and behavior.
1 - Overproduction
The Pozyx RTLS (real-time location system) identifies and eliminates overproduction by providing real-time visibility into production levels and pinpointing areas where production can be adjusted to match demand. The Pozyx solution keeps track of WIP and equipment to prevent goods lost and re-ordered, avoiding increased costs and excess inventory.
2 - Waiting
The Pozyx solution reduces waiting times by providing real-time visibility into the location and movement of materials and equipment, allowing for more efficient scheduling and coordination of resources. The Pozyx RTLS measures the waiting time of WIP to gather accurate data, to identify improvements to the production flow and to avoid downtime and that helps companies to adopt the JIT mindset.
3 - Unnecessary Motion
The Pozyx solution provides time studies and real-time visibility into the movement and location of materials and equipment, allowing for more efficient use of resources. The Pozyx analytics and dashboards indicate how motion flows can be improved, removing excessive or repetitive movements from the floor.
4 - Overprocessing
Overprocessing refers to any redundant effort in production flow that does not add value to a product. Keeping track of orders in real-time and providing accurate individual work instructions in MTO (made-to-order) environments can help to avoid unnecessary manufacturing process components.
5 - Excess Inventory
Inventory waste refers to any supply in excess of process requirements necessary to produce goods or services in a Just-in-Time manner. The Pozyx RTLS solution can locate critical inventory assets to prevent lost positions, avoiding excess stock, inventory build-up, increased storage space and higher cash flow.
Stay in the loop!
Stay up to date with the latest Pozyx and Industry news on Real-Time Location Tracking. Don’t miss out! No spam, promise.
Yes, sign me up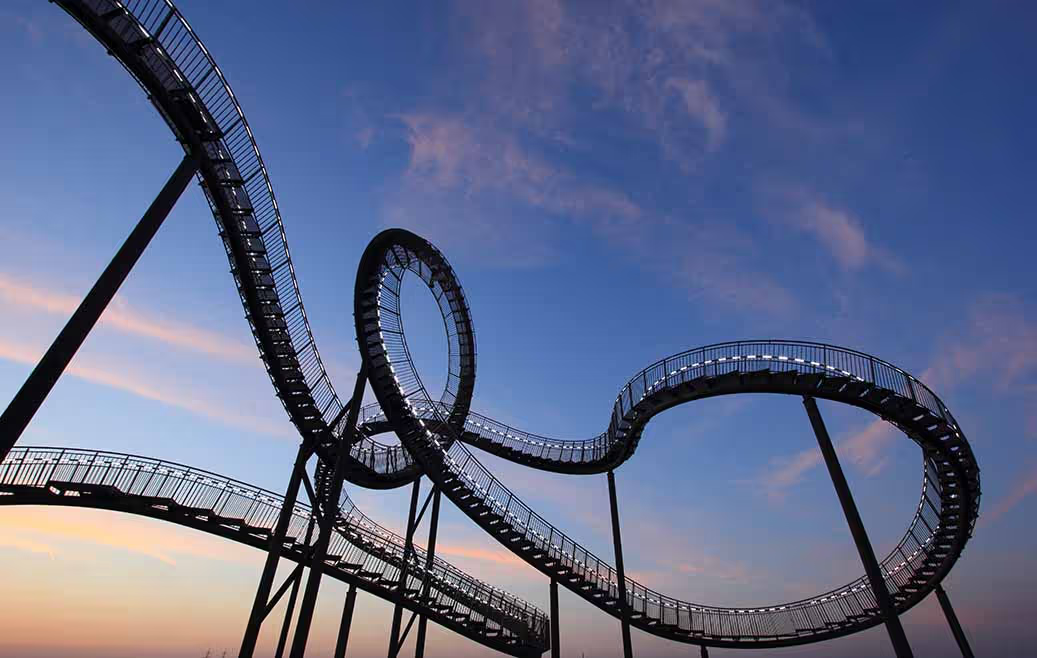
6 - Unnecessary Transport
An improper facility layout or poor workplace organization can generate transport waste. The RTLS will track and trace the transport of work in progress (WIP) or finished goods by measuring internal travel between workstations, travel between business units or even between sites. The Pozyx solution will map and analyze the distance traveled by goods, orders, and operators and detect improvement opportunities to reduce operational costs.
7 - Defects
Defective work or products can lead to loss of value due to rework, repair or scrapping activities. The Pozyx RTLS can identify and reduce defects by detecting faulty assets and deviations from the target product state or by detecting incompatible process flows. Tracking of quarantined goods will prevent the re-introduction in the production cycle.
8 - Unused talent
Underutilization of human potential can surface when employees perform highly repetitive and time-consuming jobs. The Pozyx solution generates accurate location data and reduces the need for manual time studies by industrial engineers, creating more time to spend on analyzing and improving processes, where talent can be utilized in activities such as value stream mapping that add greater value to the business.
But that’s not all. Tracking a wide range of assets on the floor and understanding their movement will add another level of efficiency improvement to the overall production process.
The effective way to reduce waste, boost profits, and achieve operational excellence
In short, the lean manufacturing system aims to maximize product value while minimizing waste without sacrificing productivity. Using the Pozyx RTLS in lean manufacturing provides accurate real-time location data of assets in the production flow.
- Pinpoint the exact location of materials and products throughout the whole production process
- Automated time studies and insightful analytics
- Optimize inventory management, avoid manual audits
- Obtain transparency on materials, reduce asset loss, and avoid goods lost
- Collect actionable data for quality control and efficiency checks•
- Plot process mapping to fuel performance metrics
- Identify bottlenecks & avoid WIP buffers overflowing
- Optimize cycle times and improve planning
The Pozyx solution helps manufacturers identify and eliminate the 8 wastes of lean by providing real-time visibility into the movement and location of materials and equipment, allowing for more efficient use of resources and ultimately leading to cost savings, improved productivity, and customer satisfaction.