Building a Smart Warehouse: Leveraging Industry 4.0 Solutions to Automate Processes
Industry 4.0 technologies and solutions developed rapidly over the last years, and now logistics and supply chain operations are becoming increasingly automated. Warehouses and storage facilities are growing smarter by using advanced technologies to streamline their operations. Those who do not invest in making their warehouse smarter, lag behind.
In this blog, we will explore how to build a smart warehouse, highlighting indoor positioning systems (IPS) and other Industry 4.0 solutions to automate processes.
What Is a Smart Warehouse?
A smart or intelligent warehouse is a warehouse where some or all processes are automated with the help of Industry 4.0 technologies and solutions. These include but are not limited to Internet of Things (IoT) devices, wireless networks, and artificial intelligence. The solutions gather and analyze large amounts of data and use it to detect patterns and make decisions about the operations in the warehouse.
The most primordial factor in making warehouses smarter is to have full visibility of the inventory and processes. Pozyx facilitates this by offering real-time tracking of assets, equipment, and people. The data can be easily integrated with ERP and WMS systems, or with other solutions used in the warehouse. This makes for full visibility of all processes in the warehouse and opens the door to automating those processes.
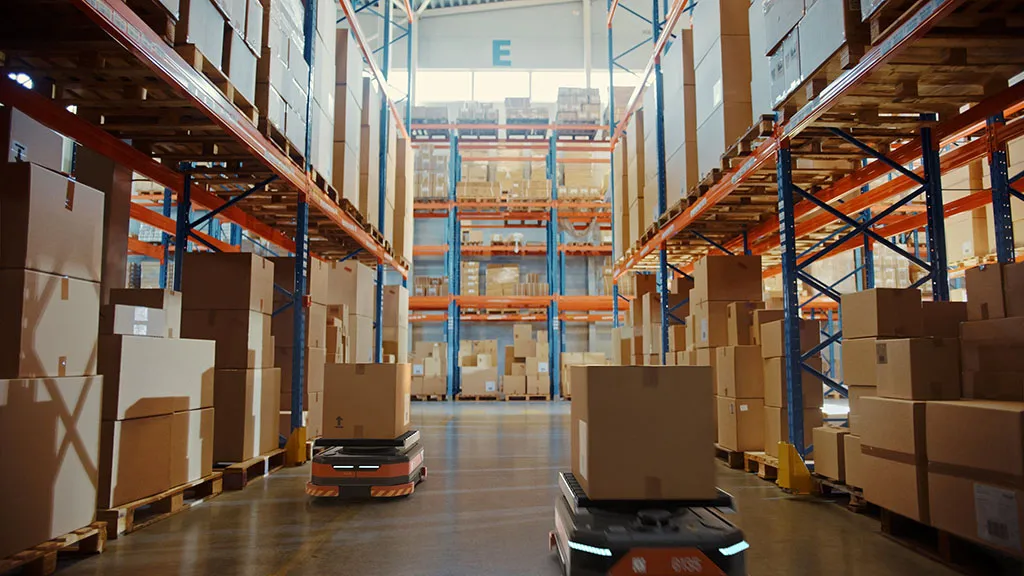
5 Benefits of Automating Warehouses
Those who invest in automating their warehouse experience several competitive advantages over those who stick with the traditional ways of organizing their warehouse. It enables faster and more efficient work and leaves less room for errors. Here are the 5 benefits of building a smart warehouse.
1. Reduced operational costs
Warehouses that automate a lot of their tasks decrease labor costs significantly while improving efficiency and reducing the number of errors to a minimum. All these factors result in notably lower operating costs and may even reduce the prices of the goods delivered to the end customer, which is an important competitive advantage in the market.
Pozyx supports efforts to reduce operational costs in different ways. By having access to real-time location data of all your assets, errors and lost assets become a thing of the past. This reduces time and money spent on rectifying errors, and searching for or replacing assets.
Stay in the loop!
Stay up to date with the latest Pozyx and Industry news on Real-Time Location Tracking. Don’t miss out! No spam, promise.
Yes, sign me up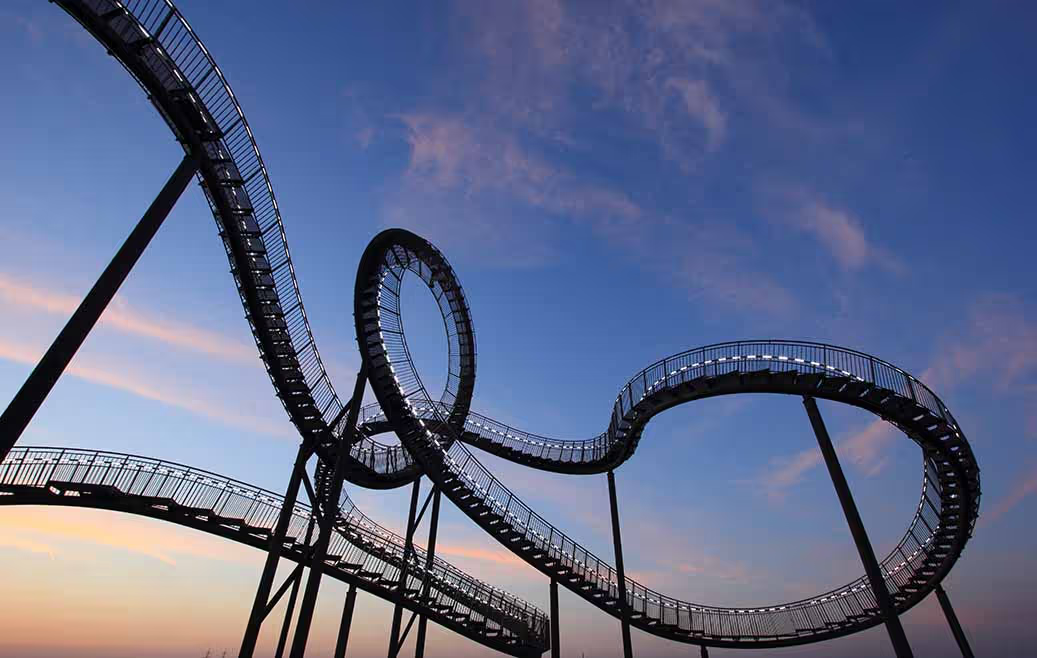
2. Faster picking and shipping
Order picking becomes easier and faster when the process is automated. Have a system plan out the optimal route and communicate that route through smart devices to the order pickers. You could even take it a step further and work with AR glasses that show dynamic routing based on optimal trajectory and calculate new routes to avoid obstacles. That is what the ART4L-Pozyx partnership is about. ART4L developed their SmartPick system that integrates seamlessly with WMS systems and optimizes order picking. Personnel gets clear instructions about which items they need and where to find them, resulting in higher efficiency and reduced stress in order pickers.
3. Better space utilization
Having full visibility of all the processes in the warehouse makes optimizing them easy as pie. That is why Pozyx offers several dashboards, time studies, and analytics to keep track of warehouse activities. Tracking assets in real-time and knowing where they are is good, but being able to make improvements based on the location data is even better.
A good example of the Pozyx Analytics that improves space utilization is the spaghetti chart. Spaghetti charts show the exact trajectory your assets and forklifts take throughout the warehouse and allow you to organize forklift routes and asset placement for maximum efficiency, without the guesswork.
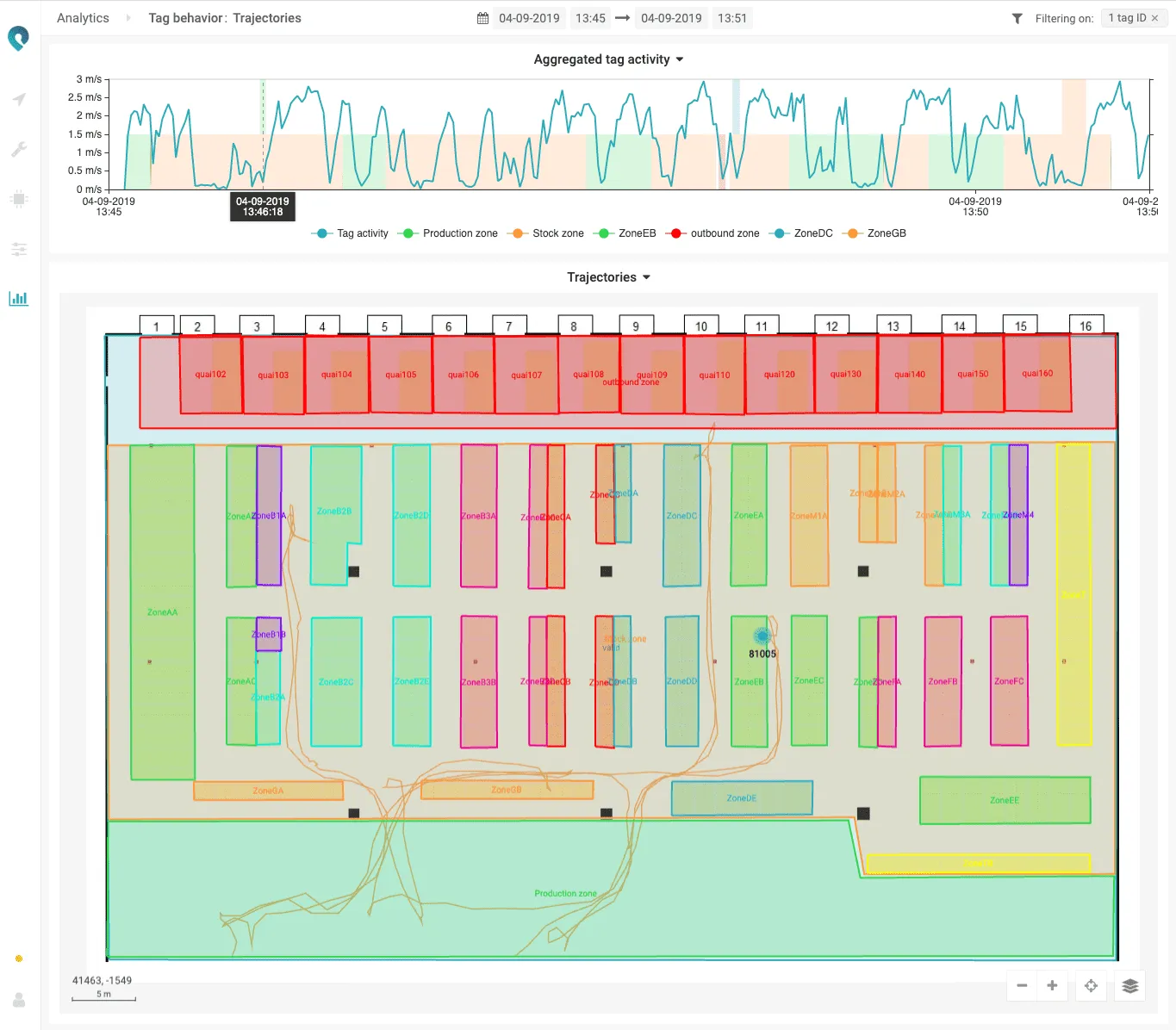
The Pozyx Platform has highly configurable dashboards to show you the information you need to reach your goals. Set clear targets on your KPIs and see at a glance where improvement is desirable. You could for example use the data spaghetti chart above to find the most efficient route and set a target on that, so that all the excess distance traveled gets logged in the dashboard. This way it becomes clear how much time and money you saved by optimizing the trajectories.
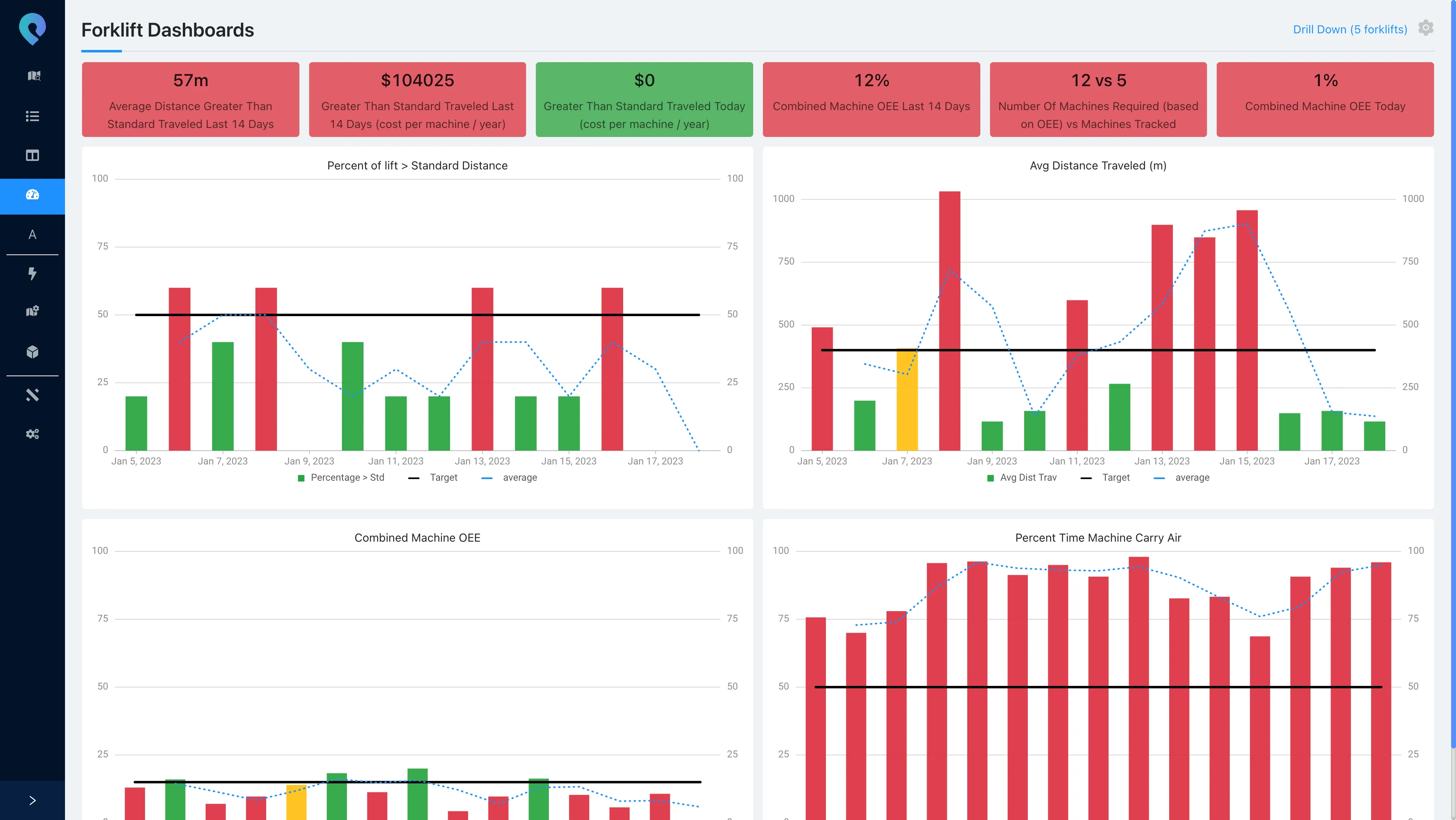
4. Fewer returns & higher customer satisfaction
Highly automated processes and accurate location information reduce the number of errors made in the picking process significantly. As a result, the customer (almost) always gets the right order and has less need to return their items. Smart warehouses also have a higher shipping rate and are able to deliver their products faster. In the end, the customer is guaranteed to get their product faster than with competitors who have manual warehouses and experience fewer wrong deliveries.
5. Overall warehouse optimization
All these factors combined make for an overall better-optimized warehouse. Streamlining and automating processes isn’t only good for the warehouse efficiency, it also beneficially affects the employees. They spend less time searching for the right goods, and more time actually delivering valuable work. The customer is also positively influenced by smart warehouses, as they have to spend less time waiting on their orders. Investing in making your warehouse smarter is a win-win situation for all parties involved.
Indoor Positioning System (IPS) in Smart Warehouses
One of the most important components of a smart and automated warehouse is an indoor positioning system (IPS). An IPS uses networks and sensors to track the location of items, equipment, and personnel in real time. This data visualizes processes and supports all five benefits of smart warehousing, improving the efficiency of warehouse operations.
Positioning systems can furthermore be used to track the movements of robots, optimize the layout of the warehouse, and help reduce errors. By leveraging an IPS, warehouse operators can gain better visibility into the operations of the warehouse. This includes the location of items, the movement of personnel, and the performance of robots and other automated systems. As a result, operators can better manage their operations, reduce costs, and improve takt time.
Pozyx offers a real-time location solution (RTLS) based on ultra-wideband (UWB) technology. With a precision of 10 centimeters and a software platform to analyze the location data, it is the ideal solution to make warehouses smarter.
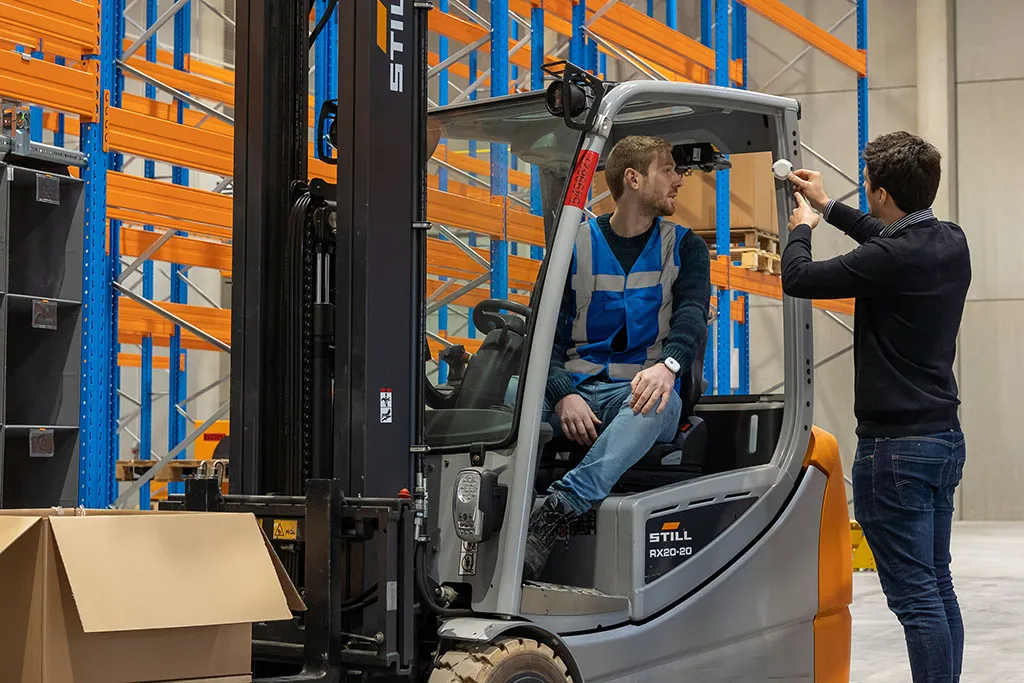
Building a Smart Warehouse
Building a smart warehouse can seem like a daunting task. It requires a comprehensive plan and the integration of multiple advanced technologies. Follow these key steps to get started at making your warehouse smarter.
1. Define the goals and objectives of the warehouse.
Defining the goals and looking at what processes need optimization is the first and most important step of building a smart warehouse. The warehouse will not be fully automated and streamlined in one day, these goals and objectives help you set priorities and make choices.
No clue on where to start? Pozyx can help you visualize and identify bottlenecks and inefficient routines, helping you set priorities and make your business run smoothly.
2. Identify actions and third-party solutions needed to reach your goals.
After setting your goals, identify the actions you need to undertake to reach them. Some actions can be taken with existing infrastructure, while others will need the integration of new solutions and technologies. Take your time choosing the right solutions for your business goals, as integrations are often high effort and will sometimes even require additional training of the warehouse personnel.
3. Integrate the technologies and solutions into the warehouse.
When you are confident you have chosen the right solutions to reach your goals, it is time to start integrating them into the warehouse. Pozyx requires only about a day to be installed and is scalable to the largest sites. It is ideal to get started with thanks to its quick setup and interoperability with WMS, ERP systems, and multiple Industry 4.0 technologies.
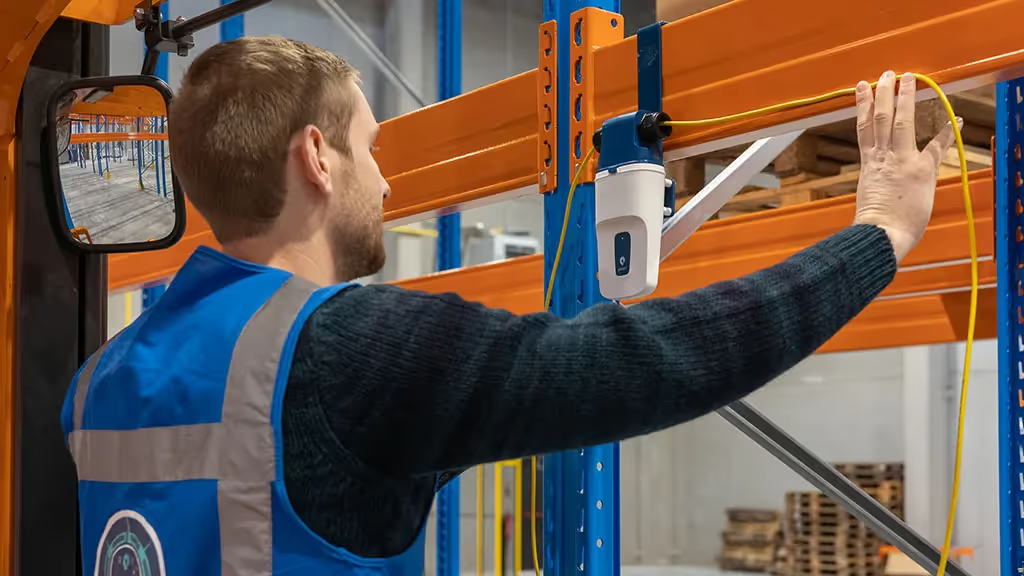
4. Collect data to test and optimize warehouse operations.
After getting started and optimizing a few processes in your warehouse, it is key to collect data and keep optimizing the operations. Work with the continuous improvement cycle: plan-do-check-act to make sure you get the most out of your investment.
Conclusion
Investing in making your warehouse smarter has numerous benefits that will give you a notable advantage over competitors. It is important to set priorities and work step by step with a continuous improvement cycle. To do this, a full overview of the warehouse processes is needed. Pozyx’s indoor positioning visualizes all assets and operations and delivers the overview you need through multiple dashboards and analytics, optimizing warehouse layout, workflow, and inventory management.
Frequently asked questions
After releasing this article, we received a number of questions that we want to clarify here as well. Thank you everyone for the contributions.
Impact on job roles and skill requirements
How does the implementation of Industry 4.0 solutions in warehouses impact the job roles and skill requirements for warehouse personnel? Are there concerns about potential job displacement due to automation?
The implementation of Industry 4.0 solutions in warehouses can significantly impact job roles and skill requirements for warehouse personnel. While automation can streamline processes and reduce the need for manual labor in certain tasks, it also necessitates a shift toward more technical roles focused on managing and maintaining the technology. There may be concerns about potential job displacement due to automation, particularly for roles that are easily automated. However, there are also opportunities for upskilling and reskilling existing staff to take on new responsibilities related to managing and optimizing automated systems.
What are some common challenges or obastacles?
While the benefits of automating warehouse operations are outlined, what are some common challenges or obstacles that companies might face during the transition to a smart warehouse, particularly regarding integration with existing systems and staff training?
Transitioning to a smart warehouse can pose various challenges for companies, including integration with existing systems and staff training. Companies may encounter difficulties in integrating new technology with their current warehouse management systems (WMS) and enterprise resource planning (ERP) systems, requiring careful planning and investment in compatible solutions. Additionally, training staff to effectively use and adapt to new technologies is crucial for successful implementation. Resistance to change and the learning curve associated with adopting new processes and tools are common obstacles that companies may face during this transition.
What are potential risks?
Are there any potential drawbacks or risks associated with relying heavily on Industry 4.0 technologies in warehouse management, such as cybersecurity vulnerabilities or system malfunctions disrupting operations? How can companies mitigate these risks effectively?
While the benefits of Industry 4.0 technologies in warehouse management are substantial, there are also potential drawbacks and risks to consider. One significant concern is cybersecurity vulnerabilities, as increased connectivity and reliance on digital systems can expose warehouses to cyber threats such as data breaches and malicious attacks. System malfunctions or technical glitches could disrupt warehouse operations, leading to downtime and potential financial losses. To mitigate these risks, companies must invest in robust cybersecurity measures, regular system maintenance, and contingency plans to address unforeseen disruptions effectively. Additionally, ensuring staff are trained in cybersecurity best practices can help safeguard against potential threats.