How Bonduelle improved its warehouse efficiency by 3%
Bonduelle, a key player in the production of processed vegetables, was looking for a way to increase its warehouse efficiency. Since employees perform countless operations per day, mistakes are both time-consuming and costly. The Pozyx ultra-wideband real-time locating system brought accuracy front and center, reducing the number of misplaced pallets. The result is a 3% increase in efficiency, saving the company hundreds of hours per warehouse, per year.
Small Mistakes Cost Time and Money
Bonduelle’s fresh packed salad factory in San Paolo Italy depends on its employees to move hundreds of loads of fresh vegetables from production lines to locations of the warehouse as quickly as possible. With over 1400 pallet storage operations per day, small errors in misplacing a pallet in the 3000 m² warehouse quickly add up. The company experienced significant time loss when pallets were misplaced and needed to be retrieved. Since time is crucial when working with ultra fresh foods, with sometimes less than 30 minutes between customer order reception to truck departure, Bonduelle wanted to be sure that pallets where stored exactly where they needed to be by controlling physically and in real time the position of the forklift drivers at storage confirmation in the WMS (Warehouse Management System). With turnaround times of fewer than 24 hours, speed and precision are vital: trucks need to be loaded on time and customers depend on Bonduelle to deliver. There is no time to look for lost products.
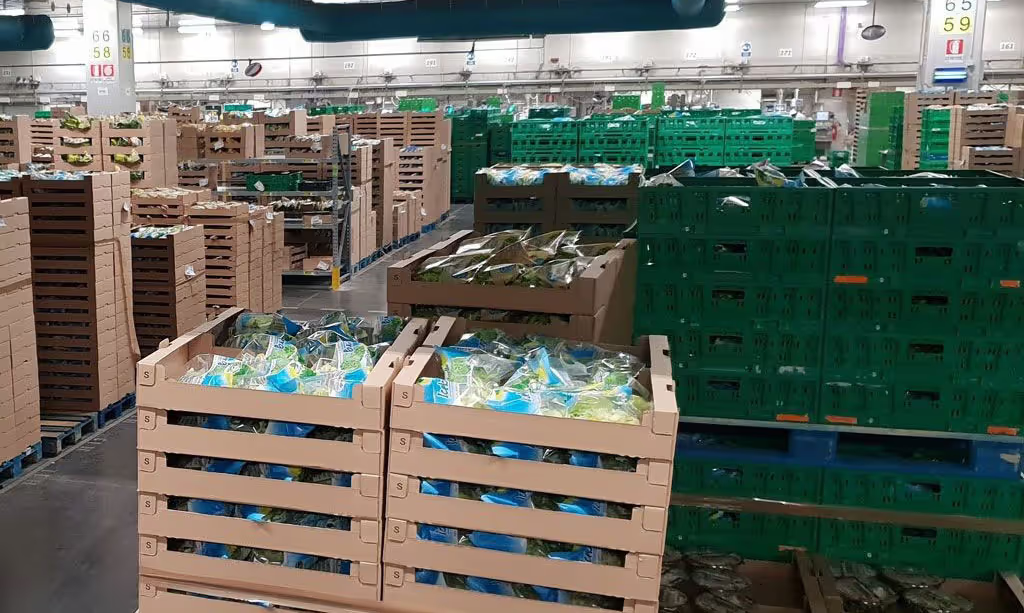
UWB Advantages Are Key
Bonduelle first experimented with other technologies to identify pallets with better precision but discovered disadvantages. Some systems take up a lot of time to install and maintain. Others required holes to be drilled in the ground, which limits the flexibility of a dynamic warehouse. What’s more, many of the lettuce bins are so small that a 15 cm error in position could be the difference between the right load and the wrong one.
Ultra-wideband technology proved to be the answer to Bonduelle’s problem, especially the Pozyx solution. With an accuracy of 10 cm, a user-friendly installation, and an experienced implementation procedure, Bonduelle had found the solution to track their pallets and the key to unlock its warehouse efficiency.
Quick Validations & A Seamless Rollout
The Pozyx prototyping kit immediately caught the attention of Bonduelle: the possibility to validate the technology quickly was a key advantage. “We had a test system up and running very easily with the advertised 10 cm precision”, says Bonduelle. The company was also impressed by how easy and user-friendly the technology was. The next step was to invite Pozyx on-site test to test the solution in working conditions.
On the positioning infrastructure side, Pozyx rapidly adjusted the technology to work seamlessly for the fresh foods warehouse. Since the environment combines 80% humidity with temperatures of about 4° C, the infrastructure was subject to harsh conditions. Pozyx eventually incorporated many of these learnings in its next-generation hardware which was released earlier this year.
UWB Accuracy Improves Efficiency by 3%
After implementing the Pozyx UWB solution, Bonduelle saw a 3% increase in its warehouse efficiency. The system’s pinpoint accuracy drastically reduced the number of misplaced pallets and bins. The company now has a real-time overview of where assets are, which saves both time and money.

That’s why Bonduelle has already implemented the system in a second warehouse in Battipaglia, Italy. What’s more, it wants to take the Pozyx solution to tackle even more challenges such as tracing the flow of raw materials and using real-time location to keep people safe in very cold working environments. For Bonduelle, the Pozyx solution is a recipe for warehouse efficiency success.