The story of how the biggest UWB application came to life
Earlier this summer (2023), one of the largest (non-consumer) applications that uses UWB location tracking was launched. In this application UWB technology is used to accurately track the location of cows inside dairy farms. This would not only allow farmers to easily find the right cow, but more importantly it provides the data for AI algorithms to accurately determine animal health or detect when a cow is in heat. With tens of barns and ten thousands of cows being equipped with this system every month, it’s arguably the largest application of UWB technology to date for a non-consumer application.
Pozyx is the proud technology provider for this application. In this article we share how this project came to life, how one demo changed the course of our company and how Pozyx transformed throughout this company-defining project.
The demo that changed everything
For the beginning of our story we have to go back to early 2017. Pozyx was less than 2 years old, we had some initial traction due to a successful crowdfunding campaign on Kickstarter and we had our first couple of employees.
After the kickstarter we received a lot of requests, and it was easy to get overwhelmed. But one requests in particular stood out. “Can your product track cows? And what is the price per tracker at a volume of 1 million units per year?“. Now, it’s not uncommon that people would exaggerate the potential for their application to get our attention. But this request came from a credible source: an international leader in dairy farming selling their solutions across the globe. Shortly after the request, we arranged a live demo at our office demonstrating our tracking solution.
We felt that this demo was important and we committed the entire (small) company on bringing this use-case to life. We transformed our office to a small barn, with cow cubicles and stacks of hay. We created some cardboard cows and attached trackers to them. One member of the team, that was particularly good at drawing, drew a barn floorplan and some cows that we used for displaying the cows on a screen, moving in real-time.
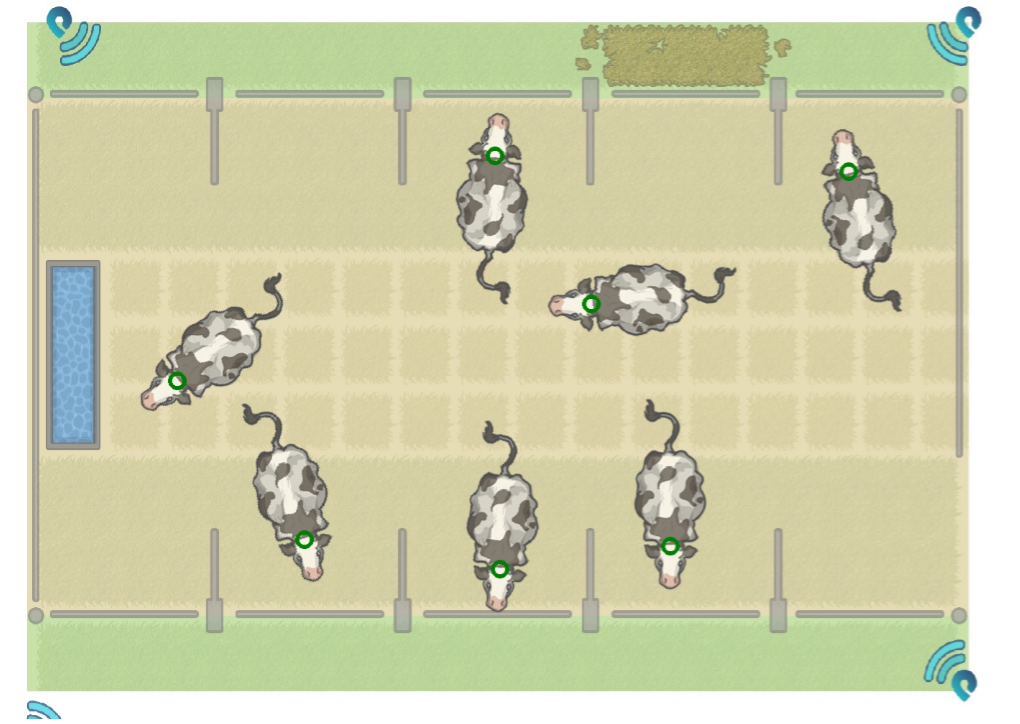
All these efforts were not in vain. The demo turned out to be a gigantic succes, with people running around acting like wild cows. Ultimately, the demo, together with a detailed proposal plan initiated a partnership that would last for years. We only learned later that we were already the fifth tracking company they had visited, but that our eagerness to work together really convinced them to continue with Pozyx, even as we were only a small startup company at that time.
Discover the Pozyx Platform
The Pozyx Platform brings indoor and outdoor positioning data together to provide full asset visibility and location-based insights for logistics and manufacturing. It facilitates warehouse and inventory control, keeps track of returnable packaging and orders, and slashes lost asset costs.
Pozyx Platform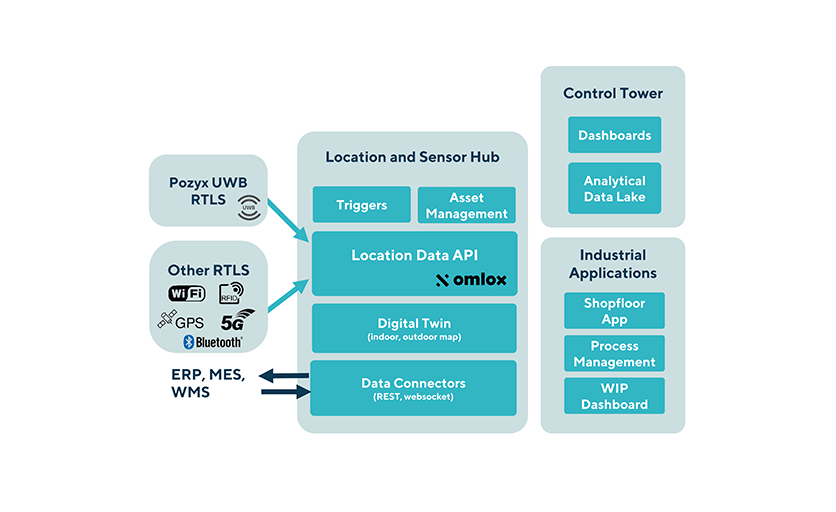
Working with a big company
To make this idea into an application, an entire team was assembled, including a software team to develop the software interfaces for the farmers, animal behavioural researchers to define the AI algorithms, project managers, supply chain managers, and of course, farmers.
At the time of our demo, our tracking system worked well to track a few tens of cows in a small area. But plenty of work lied ahead to scale this up to thousands of cows spread over large areas. Furthermore, a custom ear-tag needed to be developed which could withstand the harsh conditions in a farm, with a battery life spanning the average lifetime of a cow.
When we started this project, we were happy as a small company to even get this opportunity. We knew that once this application would launch at scale, we stood to generate substantial revenue. But until that happened, we were not selling much and were spending massive amounts of time and money on this project and all of the overhead that came with it. With some of our employees regularly being stuck in a barn for days to assist in the various tests, we knew we couldn’t continue working like this.
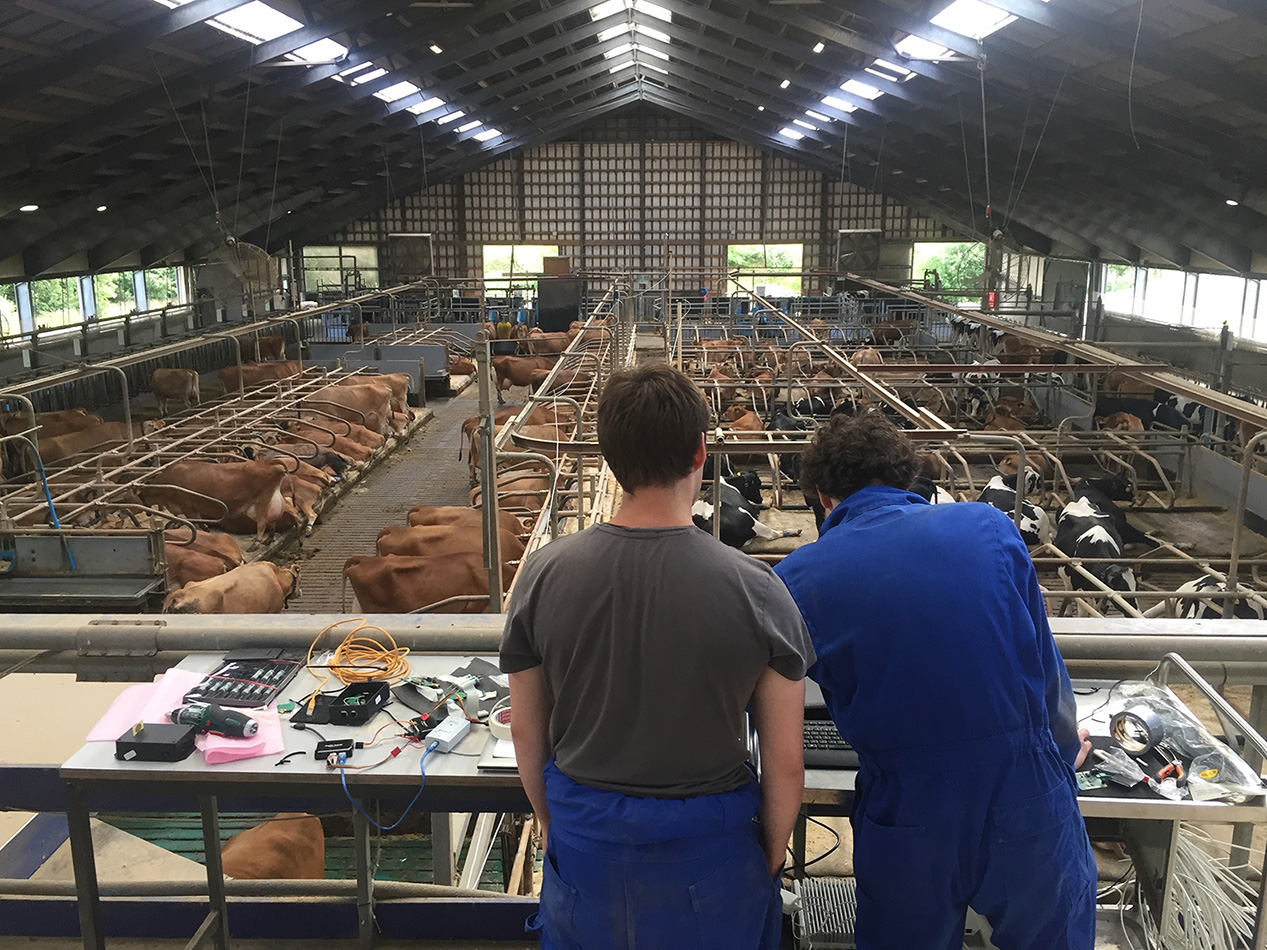
Just before the project started to suffer from it, we sat down with our partner to talk about this, and eventually settled on an agreement where all work specific to the project would be compensated for. In retrospect, this may sound logical, but as a small company being in that position, it was everything but straightforward. Ultimately this way of working turned out to work very well for both of us and resulted in a much smoother collaboration.
The definition of a pilot
With development well underway the upper management of the dairy company started to ask when the project could start piloting. It turned out that everyone had a different definition of a pilot. For us as a startup company, a pilot meant the same as a proof-of-concept, potentially with a lot of work still to do to actually launch the system. For the AI data scientists it meant tracking a large number of cows to capture the data required for reliable machine learning. For the upper management, it meant rolling out the finished product for a limited set of customers to get their feedback for marketing before doing a global launch. This meant that the product needed to be fully finished, even with the hardware fully certified, and the software and AI algorithms all working perfectly. Clearly, these different definitions did not go well together. It was in this realisation that was seen that this project would take much longer to complete before getting into the hands of the farmers.
Throughout the project, tens of thousands of cows have been tracked for several years before we even got to a pilot. Data was captured and labeled for the AI algorithms, and tested under different conditions, with different animal breeds, in different seasons. Different tracker designs were tested in the field, to evaluate which ones would damage the cow’s ear and which ones would not after wearing it for extended time. Different barns were equipped with location infrastructure, to determine standard installation procedures and guides for technicians. And large-scale robotic production was set up to produce and test massive amounts of trackers. And this all, before the first pilot got started.
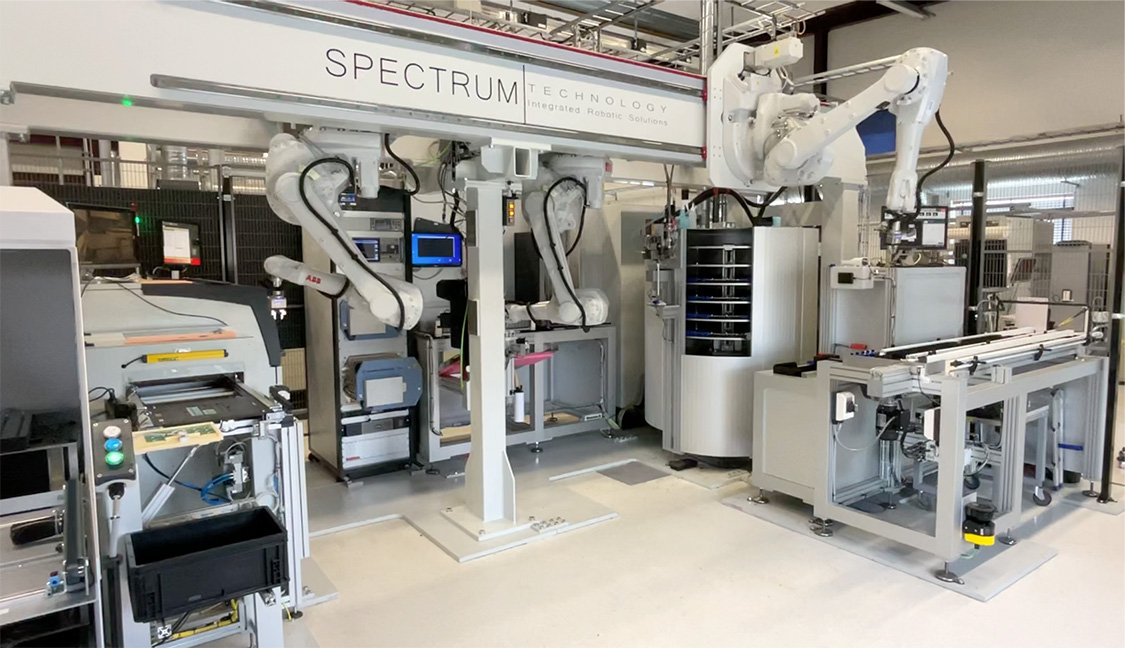
The launch
After almost 6 years of development, and successful pilots with very enthusiastic farmers, the product was finally launched. We have learned a great deal during this journey. We have become much more of a cow expert than we ever imagined. -Did you know that cows need to be impregnated before they can give milk? Who could have thought! But we also learned a lot about working together with a large company, what’s involved in bringing such a new product to the market, or how to keep investors happy when your largest project is delayed.
Mostly we feel extremely happy, and we want to thank everyone involved in this project. This list easily grows to over a hundred different people. Everyone from the Pozyx team, working diligently even when their laptops were littered with cow-excrements! The various engineers and project managers from our partner. And of course, the people who gave Pozyx the opportunity to work on this incredible application. Thank you!
The full case-study for this application can be found on our website.
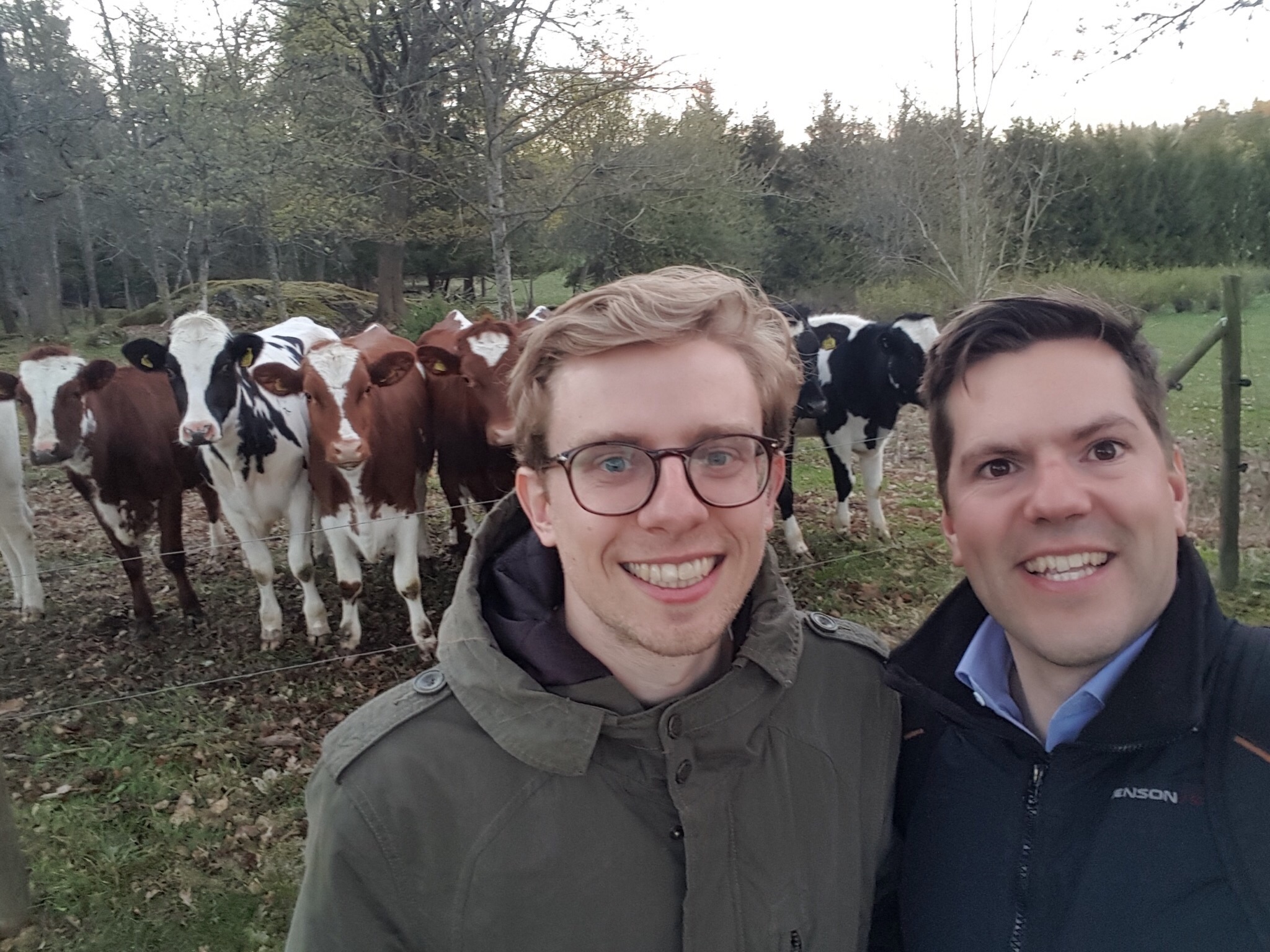
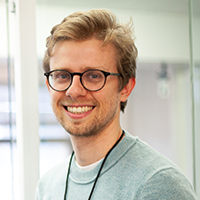
Written by
Samuel Van de Velde
CTO & Co-Founder at Pozyx
Samuel is an electrical engineer with a strong interest in location technology. Skilled in Entrepreneurship, Public Speaking, Product Management, internet of things (IoT), and Machine Learning. After graduating In 2010, he joined the Department of Telecommunications and Digital Information Processing (TELIN) to pursue a Ph.D. degree on the topic of collaborative indoor localisation. In 2015, he founded the spin-off company Pozyx out of that research.