Real-time shopfloor visibility in a job-shop through indoor positioning
Background
Salco is a Dutch company with more than 40 years of experience. Salco manufactures tailor-made door solutions. The production process is a typical example of a job-shop manufacturing environment. The production process adapts to align with every unique customer project. In its search for process improvement and quality of work, Salco has engaged with Pozyx to implement a location system, created to improve the production processes.
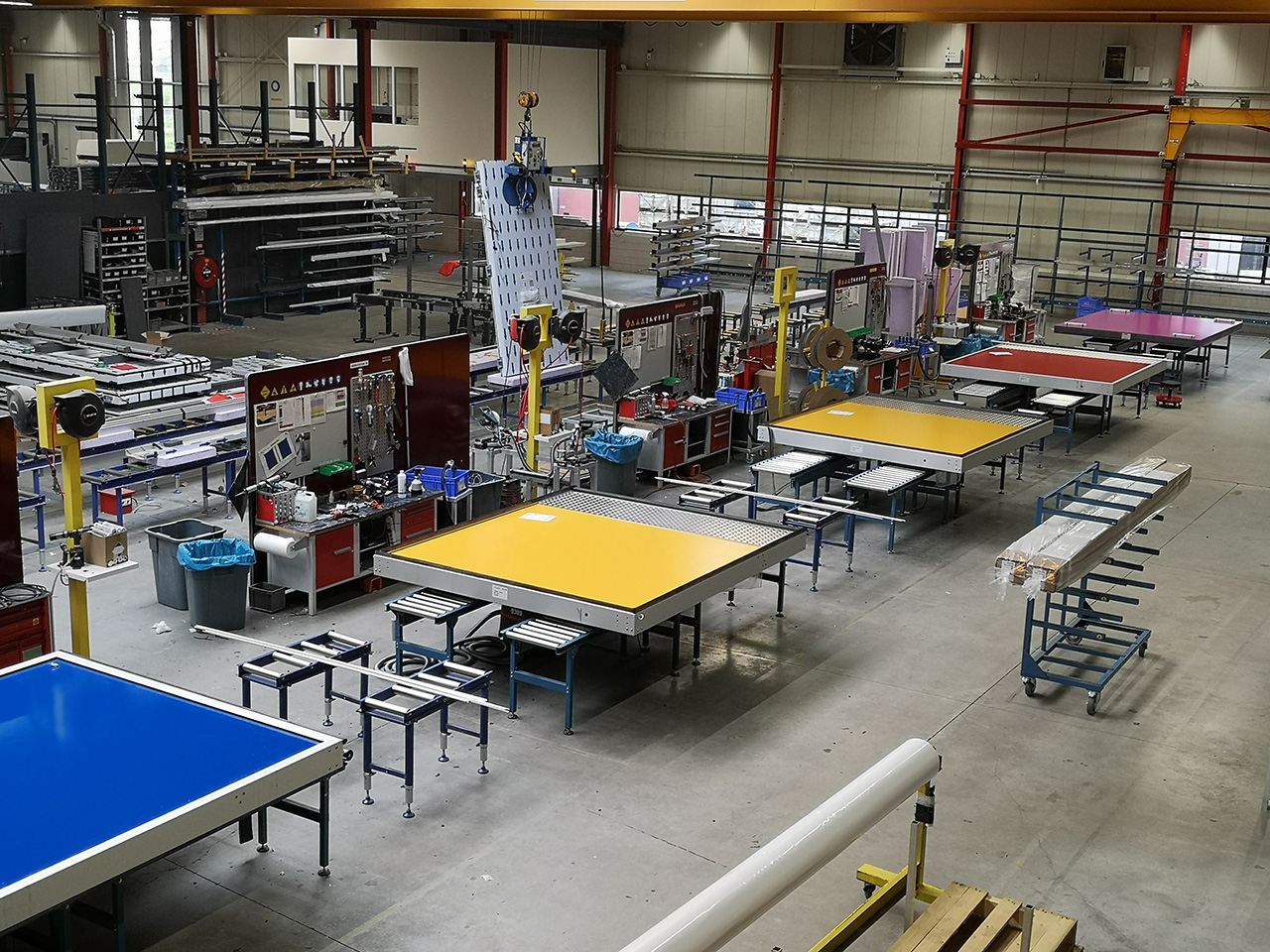
Need for shop floor visibility
At Salco, production managers are responsible for ensuring the smooth operation of production while meeting scheduled delivery targets. This involves effectively managing resources, training workers, and adapting to changing priorities. A key aspect of this role is maintaining an accurate understanding (or visibility) of the current state of the production floor.
Originally, this understanding is achieved through frequent walks of the floor, allowing managers to align work in progress with planned objectives. However, this approach is time-consuming and results in outdated information due to the duration required to cover the entire production line. Moreover, it relies heavily on the expertise of individual managers within their specific production environment, posing challenges for onboarding new personnel and providing coverage for absences.
Accurate cost calculation and Bill of Labor
As the manufacturing process at Salco heavily involves manual production steps, this manual labor constitutes a significant portion of the manufacturing cost. Due to Salco's commitment to providing customers with a high degree of product customization, accurately determining labor costs (Bill of Labor) for every potential product combination becomes challenging.
“Today we do not know exactly the production times for each production step. Hence, we cannot know what the labour cost details are, where possible inefficiency can be found and cannot control profitability on product level.”
Quote Jan Heddes - General manager at Salco
Accurate measurement of processing time
On a High-mix & Low volume type of production, it is challenging to get a high efficiency of the production lines when there is a mix of products with different processing times along the same process flow. Measuring with high accuracy the processing time at every workstation level for every individual product was extremely difficult, but this task is performed automatically when the product has a positioning tag attached. The Pozyx platform can deliver these accurate measurements for improving the planning of the optimum product mix and overall efficiency of the production process.
How an RTLS was used on the shop floor
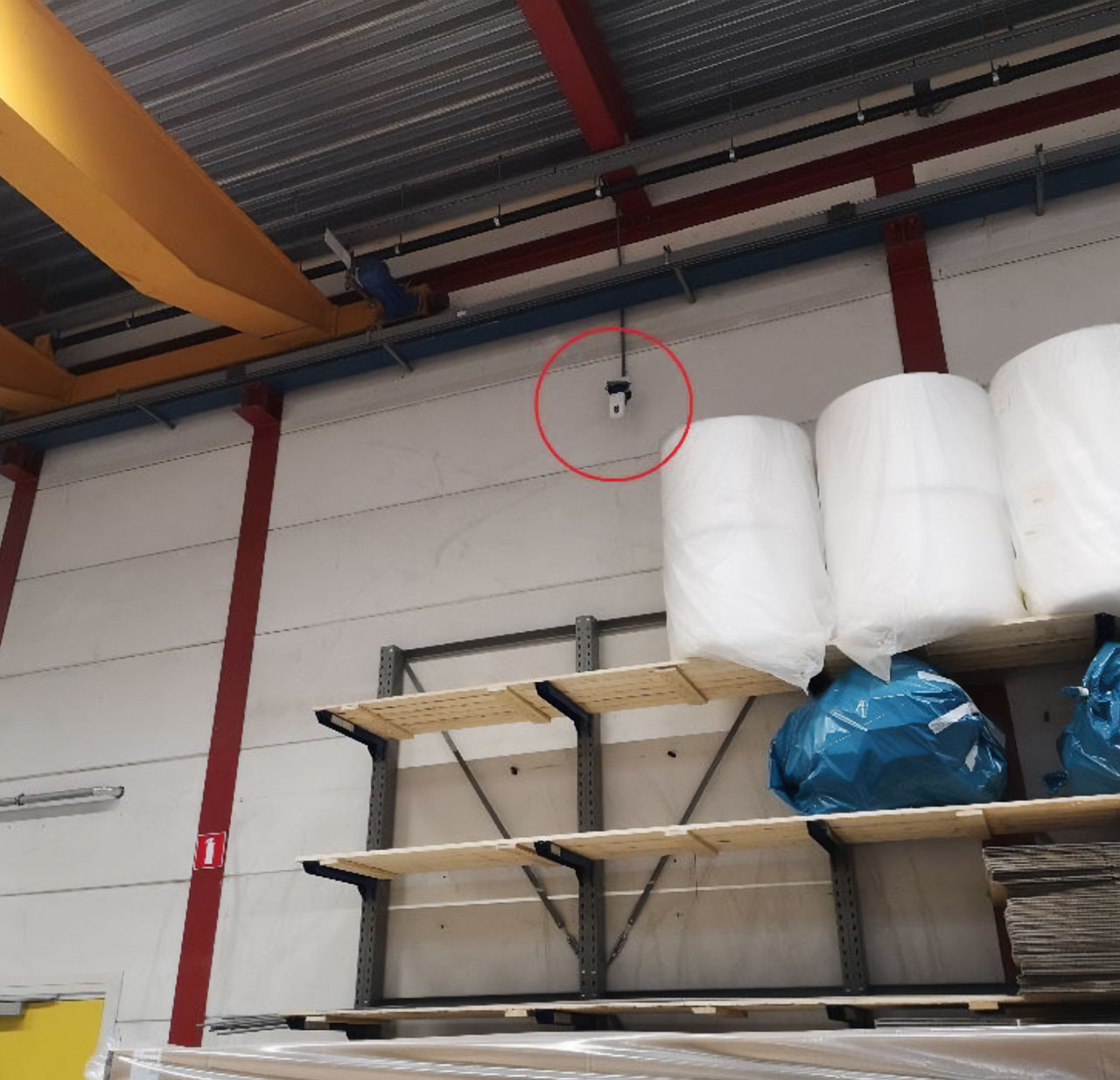
In order to obtain more visibility and data for cost calculations, Salco considered several approaches. Initially, it was considered to add scanning codes to working instructions and tasking operators to scan these codes on every step. However, this would add a non-value adding procedure that also does not bring any value to the operator themselves. On top of that all, it’s also very error prone.
Rather, Salco opted for using an accurate indoor real-time locating system (RTLS). This would not require any additional steps for the operators except at the start and end of production to attach a tag to the order. With the Pozyx UWB RTLS it is possible to accurately track hundreds of assets up to 10cm. Because of the real-time nature of the system, the RTLS would always represent the actual state with no errors. To cover the two buildings, 22 fixed sensors (called anchors) were installed on the walls.
A tag is physically attached to something that is moving and is an important part of the process. The most important moving things in the process are:
- Product components (examples: panels, doorblade profiles, frames).
- Transportation devices (carts).
- Operators which are working on the product components.
In total, around 500 tags are used.
The Pozyx Platform
While the RTLS system provides the location data, the Pozyx platform offered a user-friendly application to leverage the location data. The application allows to configure the different production processes whereby each production step is represented by a specific area in the building. By detecting if a tag is inside a specific area, the status of a product can be updated.
The platform was connected to Salco’s ERP in order to match all product order information with a specific tag. Whenever a production order was launched, a tag was linked with the order and added to the paper instructions that travel together with the order through the manufacturing step. At the end of production, the tag is automatically unlinked by moving it in a specific area. This way the tags can be reused for subsequent orders.
More advanced features offered by the platform are buffer warnings whenever the buffer amounts reach a certain value, alerts when workstations are abandoned for too long, reporting for cost calculation and analytics for value stream mapping.
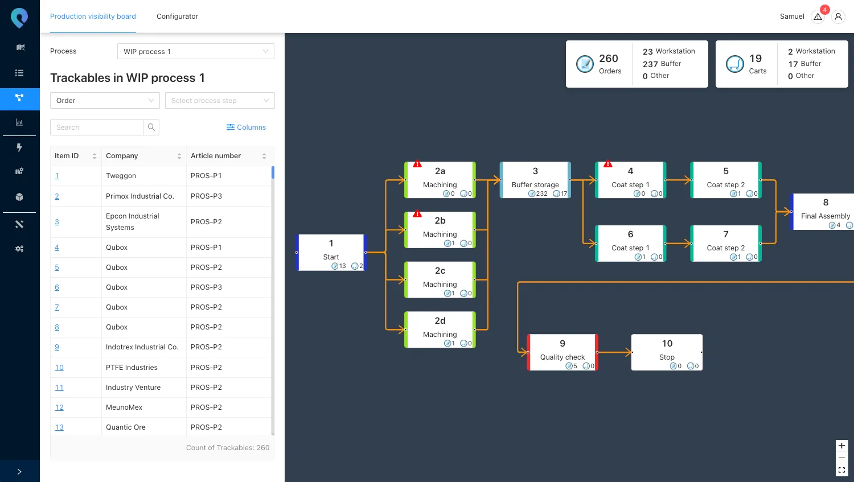
A fully automated Kanban system is implemented along the production process using the functionality of custom defined triggers in the Pozyx platform. This functionality takes advantage of real time monitoring of all buffers and generates automated requests for the associated workstations to deliver the right amount of products at the right time. Achieving a smooth pull-flow without gaps and without bottlenecks is now possible without human surveillance. More than this, it is possible to get real time alerts and diagnosis on the full-scale of the production process, even when it is spread across multiple buildings or locations.
Operator tracking and privacy concerns
In consideration of EU and Dutch privacy laws, special consideration was taken on the tracking of the operators in relation to the protection of personal data of employees. More specifically GDPR – General Data Protection Regulation EU 2016/679 and the implementation of this in the Netherlands (Uitvoeringswet Algemene verordening gegevensbescherming).
Specific to workers, the system was configured that a tag used by operators is not linked to a certain operator. These operator tags are all available at the beginning of the work shift, and any operator can pick any tag to carry around during work hours. They can even change tags during work hours. Tracking only happens within the relevant working areas of the building.
The software system uses the positioning data of the anonymous operator to measure the work time added to a certain product, and for this purpose any identification of the operator is unnecessary. It is important to accurately measure how much work time is added, not who added this work time.
The identity of the operators who made these work times is not known, because this system has no access to get or to process any personal data that can identify the operators.
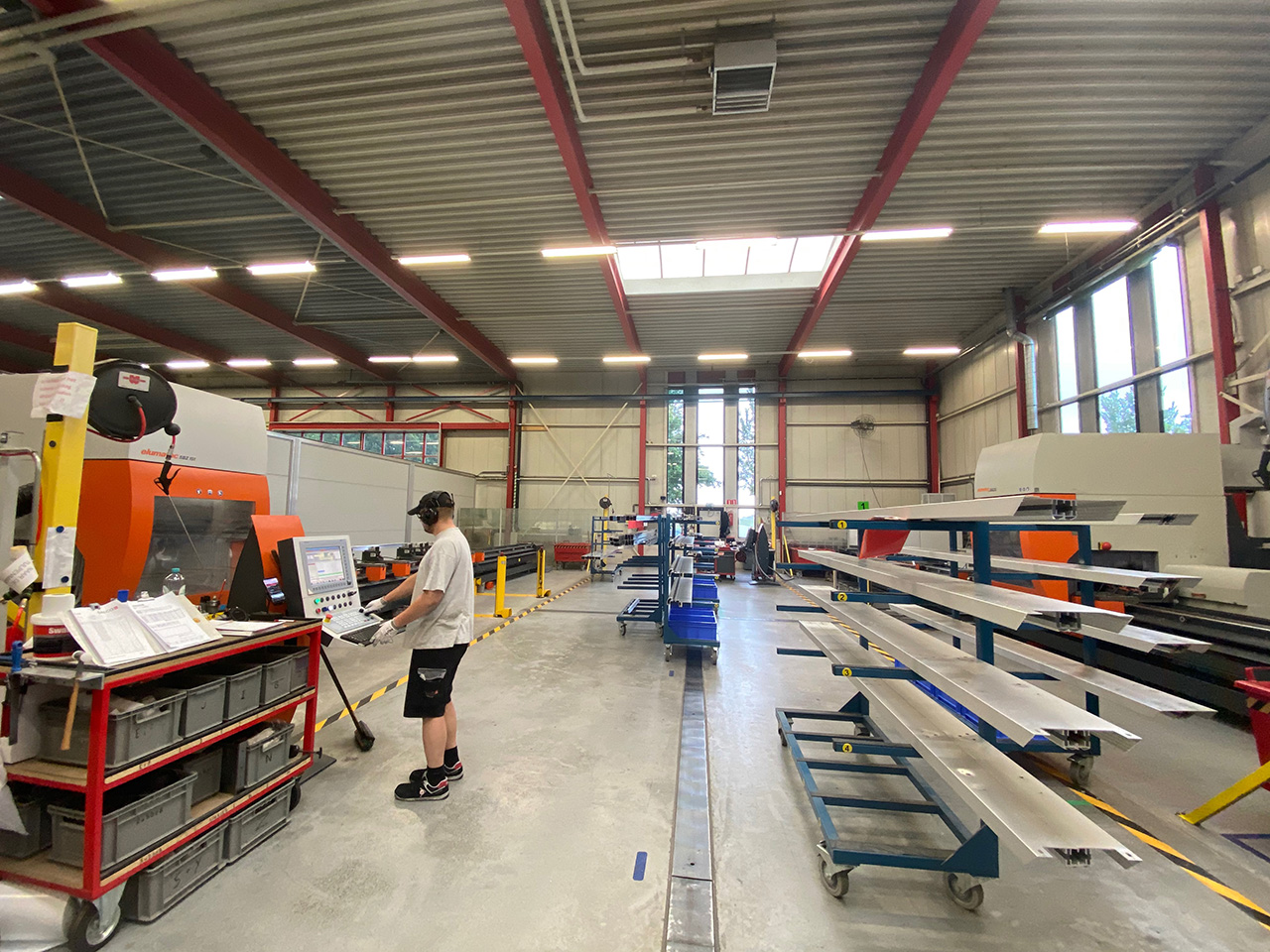
Conclusion
By implementing this system, Salco managed to obtain better visibility on the status of the work in process on its shop floor and obtain the data required for cost calculations. Some of the benefits achieved:
- >50% reduction in delay in detecting production flow abnormalities
- >50% reduction in time spent on the factory floor by the production manager to monitor the progress
- Improve the cost calculation with a better estimation of worktime per product (20% better estimation).
- > 20% reduction of the wasted time caused by bottlenecks or gaps in the production flow.
Looking to add real-time visibility to your shopfloor?
Look no further! Schedule a call with our experts to discuss your use-case, we are happy to help!